Ou “Panels et rétro-éclairage, l’apport d’une graveuse laser”…
Dans les 2 précédents volets de ce sujet, je vous ai présenté 4 formules et 2 variantes pour rétro-éclairer les panels du simu ; le résultat a été au rendez-vous, mais au prix d’une réalisation très délicate.
Pour mémoire, l’objectif est d’obtenir une gravure du panel bien blanche sans rétro-éclairage, uniformément lumineuse avec rétro-éclairage ; à cela, il faut rajouter une intégration compacte des composants qui équipent le panel : switchs, boutons poussoirs, potentiomètres, afficheurs 7 segments, etc, et la connectique pour relier ce panel à l’électronique de commande du simu.
Les graveuses laser en provenance de Chine ont atteint des prix tout à fait dérisoires, j’ai finalement décidé d’en acquérir une et de la mettre à profit pour élaborer une 5ème version de panel ; je vais en profiter pour détailler la fabrication complète d’un panel, il s’agit d’un panel de services, qui permet le remplissage des réservoirs de l’A320, l’ouverture/fermeture des portes (c’est ce qui déclenche la sonorisation interne de la cabine), et le push-back (au sol, repoussage de l’avion pour le mettre en position d’avancer par lui-même).
1 - Une graveuse laser d'entrée de gamme :
1.1 - La machine :
De nombreuses petites machines sont apparues sur le marché, j’ai choisi une Ortur Laser Master 2 équipée d’un laser diode de 15w, ce qui est suffisant pour les travaux de gravure sur bois, plastique, carton, …, ainsi que pour la découpe de papier, carton, balsa, et autres matériaux fins et tendres.
La conception de la machine me semble correcte, entrainement par courroies, une pour la tête laser, et deux autres pour le portique ; les poulies d’entrainement des 2 cotés du portique sont solidarisées par un axe, ce qui est essentiel pour garantir le maintien de la bonne géométrie du tout.
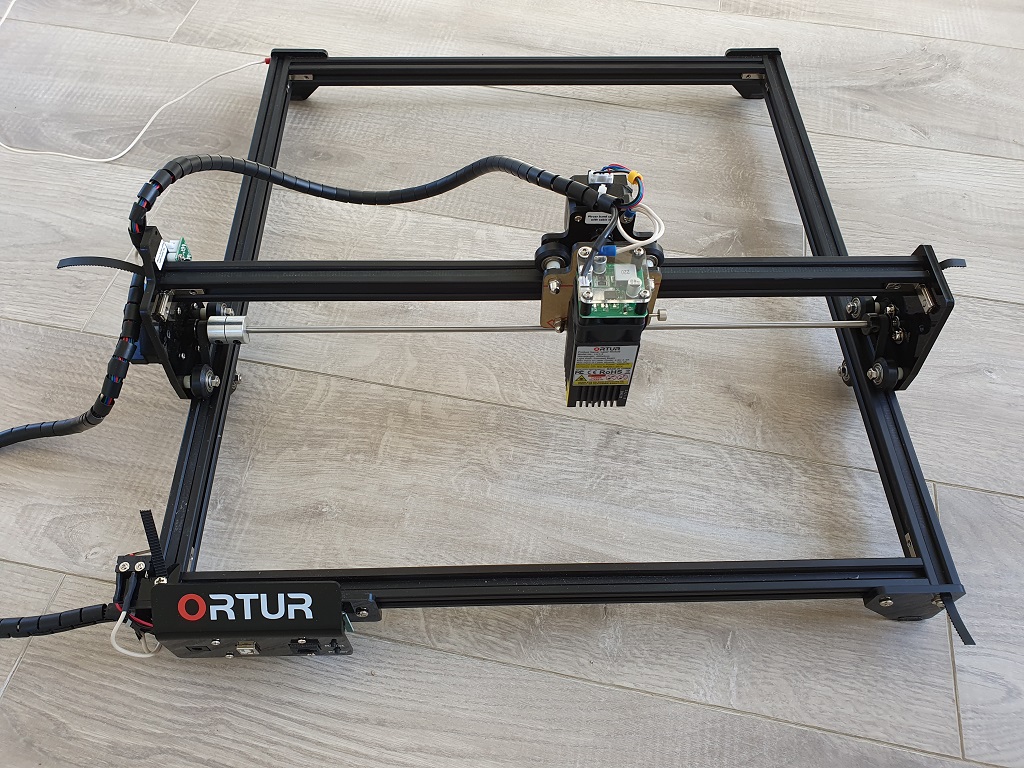
La machine est livrée en kit, quelques profilés alu pour la structure, des pièces d’assemblage essentiellement en plexi et métal moulé, 2 moteurs pas-à-pas, un faisceau de cables, courroies crantées, poulies et visserie, une platine de commande equipée d’un processeur 32 bits, un laser 15w (15w consommés, puissance effective de l’ordre de 5w) , une paire de lunettes de protection et une documentation.
L’assemblage est simple, un bon quart d’heure suffit ; les branchements sont à l’identique, un cable d’alim (alim 220v AC/12v DC), et un cable USB vers l’ordinateur, en l’occurence un PC sous W10.
2 logiciels accompagnent la machine, LaserGRBL, gratuit, et LightBurn en version d’essai ; j’ai essayé les 2, et ai rapidement opté pour l’achat du second, qui me semble particulièrement riche et simple d’utilisation : il est doté d’un éditeur graphique mais permet également d’importer des dessins déjà prêts (en particulier au format .dxf, ce qui est impératif à mes yeux, car le dessin de mes panels est réalisé avec un outil de CAO – Solidworks ou Turbocad), et permet une attribution des paramètres de gravure/découpe par le biais de calques.
La prise en main de LightBurn est très rapide, les premiers essais peuvent intervenir dans le 1/4h.
1.2 - Essais :
Avant tout, et ne connaissant pas les caractéristiques des lunettes livrées avec la machine, j’ai préféré commander d’autres lunettes, certifiées pour la longueur d’onde du laser.
Pour les essais, il s’agit de vérifier si les objectifs que je me suis fixés sont atteignables : il faut à minima graver un panel en PMMA (plexi) recouvert de peinture blanche, puis de peinture grise, en ne retirant que la peinture grise, et en laissant apparaitre la peinture blanche (et qui doit rester blanche).
Annexement, j’aimerai mettre à profit le laser pour la réalisation de PCB.
– Premiers essais, basiques, gravure sur mdf : une matrice test, avec un double balayage des 2 principaux paramètres de gravure, puissance et vitesse, permet de rapidement prendre ses marques. Je retiens une bonne formule, vitesse 1500 mm/mn, puissance 80% ; il faut noter que la vitesse max de la machine est affichée à 3000 mm/mn.
Un second test, sur un petit panel test, découpé à la cnc, puis gravé au laser, montre une bonne concordance entre la géométrie de ma cnc, plutôt éprouvée, et celle de la graveuse.
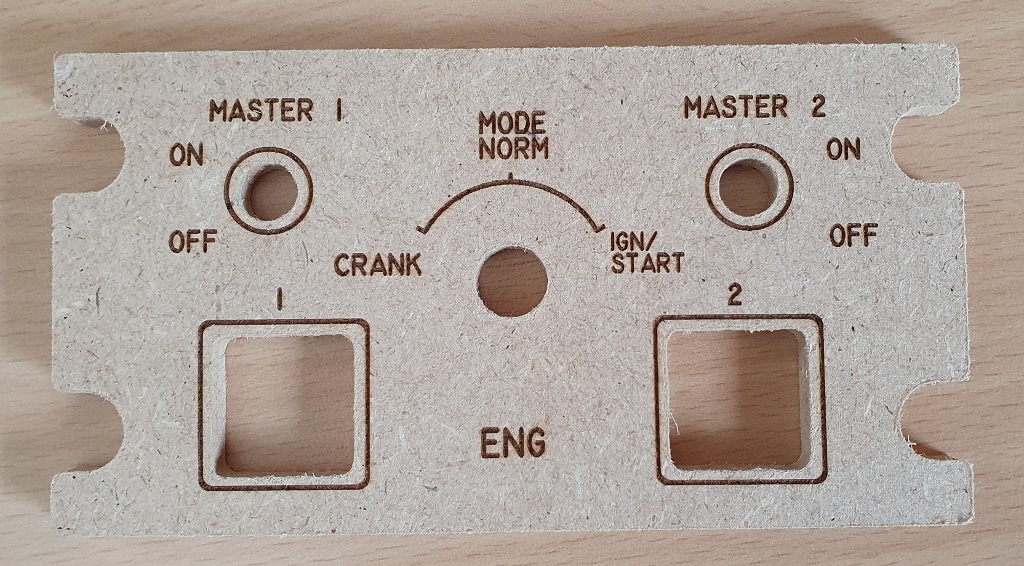
– Seconds essais, vraiment le truc important : le panel peint en blanc puis en gris, la gravure doit laisser la couche blanche bien visible et toujours bien blanche.
Quelques amateurs dans le monde de la simulation aéronautique s’y sont essayés sans succès jusqu’à présent, mais il semble bien que ce soit à la fois une affaire de type de laser, et de type de peinture ; c’était sans compter sur un fan du club, aussi branché que moi sur l’atteinte de ce grall, et qui à force de tests, à découvert le couple gagnant, c’est dans sa roue que j’ai instantanément sauté pour finaliser le process – merçi FX (François Xavier Wiart, Fix sur le forum Air Cockpit), l’acharnement finit souvent par produire ses effets !.
Ce couple gagnant semble être laser diode et peinture blanche électroménager (décrite comme “laque blanche émaillée”).
J’utilise donc du PMMA transparent, recouvert de 2 couches de peinture blanche, et de deux couches de peinture grise (peinture auto). Même procédé que la première fois, et très rapidement j’obtiens enfin le résultat tant désiré, environ 1500 mm/mn à 20% de puissance, et 2 passages offrent la gravure de rêve !
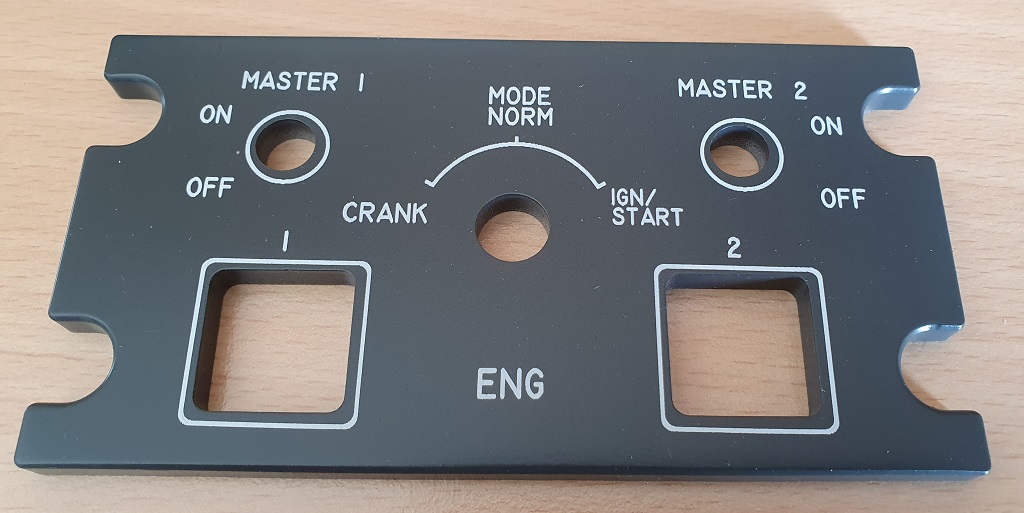
– D’autres essais, la réalisation de pcb :
Après avoir longtemps pratiqué les procédés classiques (masque photo, pcb recouvert d’un vernis photosensible, insolation, gravure au perchlorure de fer), je suis passé à la gravure à l’acide chloridrique (gravure plus précise), puis, grace à la cnc, à la gravure à l’anglaise (qui reste assez lourde, levelling obligatoire pour composer avec les variations d’épaisseur du pcb).
Le procédé par insolation demande des masques de bonne qualité (en général, impression jet d’encre, ça n’est pas parfait), et une parfaite application du masque sur le pcb (afin de minimiser les phénomènes de diffusion autour des contours) ; au final je n’ai jamais été totalement satisfait.
La gravure anglaise donne de bons résultats, mais présente ses limites lorsqu’il faut graver fin (phénomène de repoussage du cuivre lors du passage de la fraise) ; ce procédé peut en outre devenir long (la chaine de production du tracé des contours des pistes est lourde, le temps de gravure est vite important).
Je vais tester la gravure du masque directement sur le pcb : pour ce faire, peinture noire du pcb (peinture auto), et import du tracé du pcb au format .dxf. La gravure de la peinture n’est pas, de prime abord, très emballante, les zones gravées restent assez grises et donnent l’impression de ne pas être complètement débarassées de la peinture. Mais un passage à la gravure chimique (un mélange, dans l’ordre, d’eau – 1 vol, d’HCl concentration 30% – 0,6 vol, et d’H2O2 130 vol – 0,3 vol)) dévoile un résultat très satisfaisant.
Sur l’éprouvette ci-dessous, si on regarde la gravure la plus rapide (en haut à droite, 2900/80 0.05), de haut en bas et de gauche à droite :
– les 3 pistes horizontales du haut : largeur et espacement 0.375
– juste en dessous, on devine 3 autres pistes, pratiquement disparues : 0.250 (l’espacement des lignes de balayage est de 0.05, pour des pistes de 0.250 c’est hyper limite)
– les 6 pastilles avec 2 pistes horizontales : pastilles diam 1.8 à droite, 1.6 à gauche, espacement 2.54, pistes 0.400
– les 3 pistes verticales juste à droite : 0.500
– les 4 pistes horizontales en bas : 2 pistes .750, 2 pistes .500
– Le tracé plus conventionnel : pistes de 1
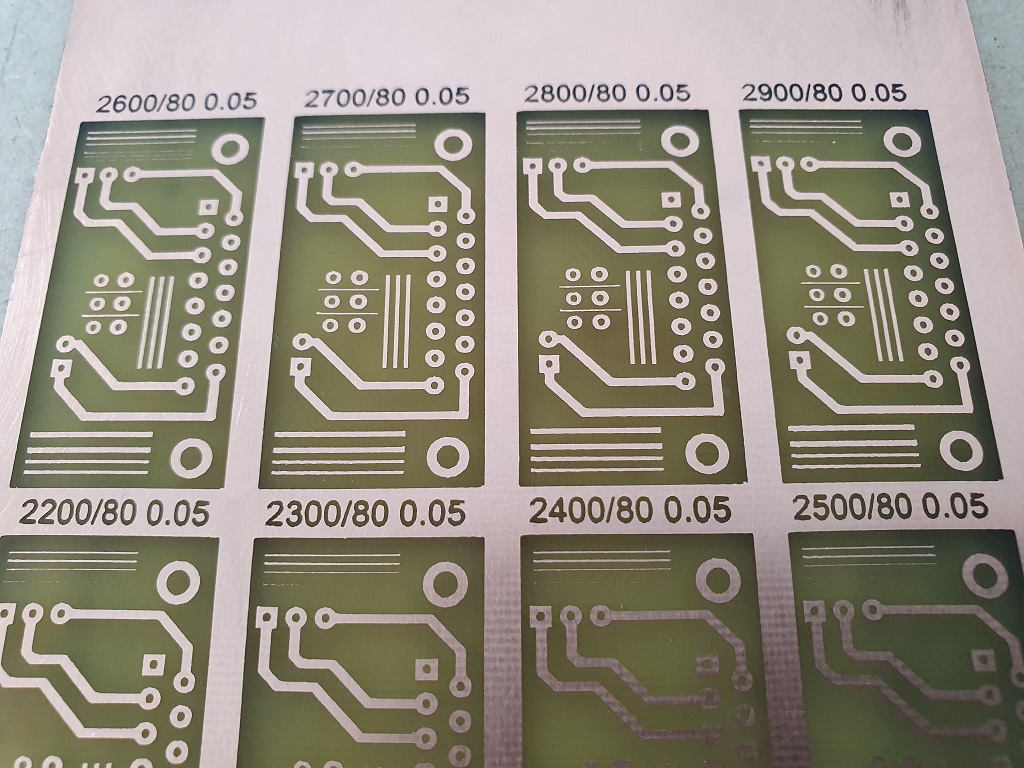
Le plus rapide étant le mieux, je retiens les paramètres suivants : vitesse 3000 mm/mn, puissance 80%, et espacement des traces 5/100 (et non 10/100).
Il faut noter que, le faisceau laser n’ayant pas un diamètre nul, la taille des divers tracés est un peu réduite – théoriquement une amputation d’un rayon du faisceau, il faudra tenir compte de ce phénomène.
Le résultat est vraiment concluant, tracé précis, pistes parfaitement intactes (pas de micro-perforation) ; au passif du procédé, gravure laser longue (près d’une heure pour l’éprouvette), et les trous restent à percer (ce qui n’est pas le cas avec la gravure à l’anglaise, très appréciable). Reste à vérifier ce que celà donne pour un double face, la géométrie de la machine est-elle correcte ? (orthogonalité X/Y impérative).
1.3 - Quelques ajustements :
La machine n’est pas chère, des ajustements s’avèrent très vite nécessaires, sinon indispensables !
– La géométrie :
Si l’on souhaite une bonne précision – gravure sur une pièce découpée sur une autre machine, typiquement une cnc, ou gravure recto-verso comme pour les pcbs double-face – il est impérieux de s’assurer que les axes X et Y sont bien orthogonaux.
De base, l’orthogonalité est assurée grace à 2 équerres en métal injecté qui assurent la liaison entre les flans du portique et le profilé alu de ce dernier, et 4 équerres qui assurent la liaison entre les profilés latéraux qui constituent le cadre. Le résultat est correct mais sans plus, il est utile d’apporter d’éventuelles corrections à l’aide de cales calibrées. Je pense plus tard rajouter des équerres plus importantes et placées sur les profilés (et non dans l’angle des paires de profilés), ce qui rendra les réglages bien plus rationels ; idem entre le profilé du portique et les flans, moyenant leur remplacement.
Il faut également prendre garde à ce que la tension des 2 courroies latérales ne contraigne pas l’orthogonalité du portique (il faut retoucher la fixation des courroies de façon à permettre un réglage fin).
– Toujours la géométrie :
Le positionnement précis des pièces à graver n’est pas simple, la reproductibilité du 0 machine n’étant vraiment pas assurée. J’ai opté pour la méthode suivante :
Je fais précéder les opérations de gravure par une première gravure (donc en tout début de job) du contour de la pièce à graver,”agrandi” de 2/10, et d’une petite figure quelconque en dehors de la zone à graver ; ainsi, lors du lancement des opérations, j’interromps la gravure lorsque qu’elle atteint la figure, puis positionne la pièce à graver dans le contour qui vient d’être gravé, et poursuis la gravure.
Cette façon de procéder est un peu délicate mais efficace ; il faut cependant s’assurer que le faisceau laser est parfaitement perpendiculaire au plan de travail, sans quoi l’épaisseur de la pièce à graver induira un décallage par rapport au cadre de positionnement. Une façon d’approcher ce réglage est de considérer que le faisceau laser est bien parallèle aux faces latérales de la tête laser ; à partir de là, 2 équerres le long de 2 flans adjacents de la tête permettent de retoucher les divers fixations de la tête et du profilé du portique.
Sur le modèle 15w de cette machine, la focale du laser est fixe, le laser est monté sur une petite glissière à queue d’arronde en alu dont la position est arrétée grace à une vis portant sur l’arrête de la queue d’arronde ; ceci induit évidement une grosse imprécision de positionnement, je remédierai à celà à l’avenir ; pour l’heure, j’ai bloqué la queue d’arronde pour figer mes réglages, et assure le réglage de la focale grace à des jeux de cales placées sous la pièce à graver, en fonction de son épaisseur.
– La fumée :
Son évacuation s’impose rapidement, que ce soit pour des raisons d’efficacité ou de simple salubrité. J’ai opté pour un coffret en mdf de 6, équipé d’un extracteur d’air d’une puissance de 25w (GSB) et d’un conduit d’extraction d’air souple – attention, un simple ventilateur de PC ne suffit vraiment pas.
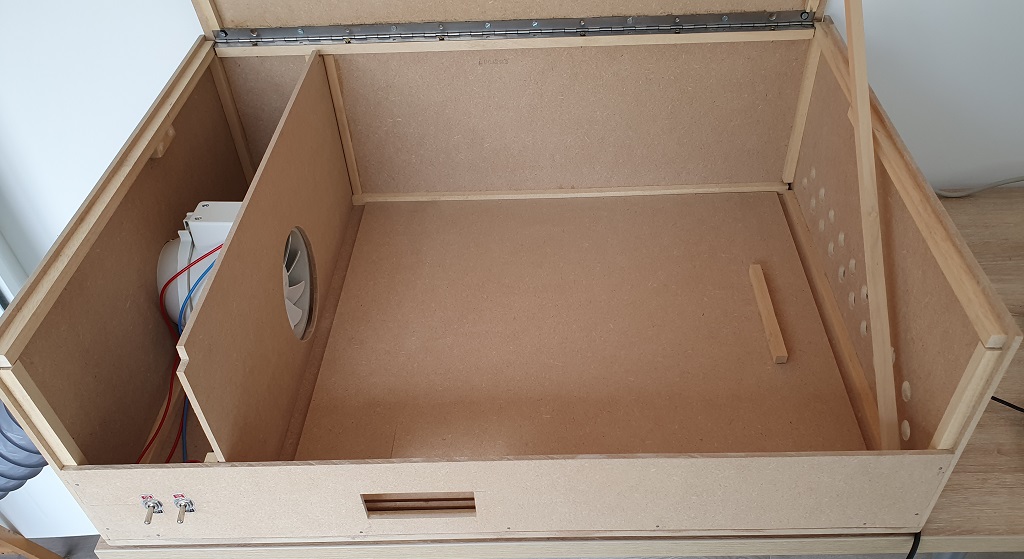
J’en ai profité pour équiper le couvercle d’une plaque de PMMA orange transparent, réputé protéger de la lumière du laser, ce qui n’exclut pas le port des lunettes de protection !
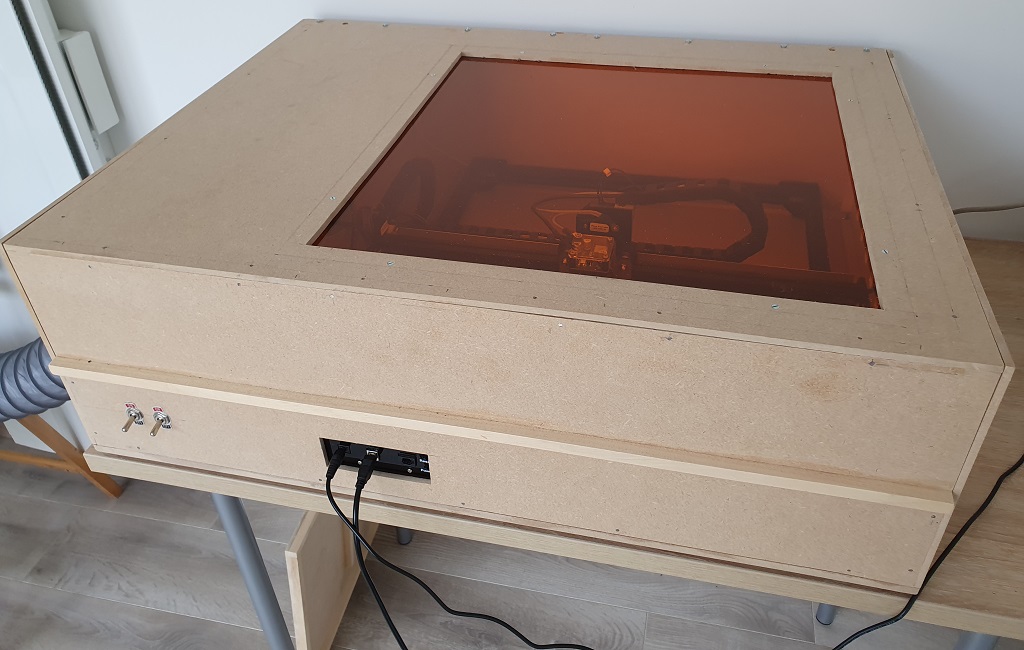
– L’installation électrique :
Le portique ainsi que la tête laser se déplacent sur les profilés latéraux et celui du portique grace à des roues en matière synthétique, il n’y a pas mieux pour générer de l’éléctricité statique, l’électronique déteste celà ; il est donc vraiment utile de rajouter une mise à la masse de tous les éléments mobiles : tête laser, chariot laser, portique, platine de commande, chassis ; le tout doit ensuite être relié à la terre.
– L’installation éléectrique encore :
Le faisceau de câbles, qui va de la tête laser et du moteur du chariot laser d’abord, au moteur du portique et du fin de course embarqué ensuite, puis enfin à la platine de commande et au second fin de course, est simplement gainé d’une enveloppe souple plastique ; il n’est pas vraiment très souple, et contraint le mouvement de la tête laser à proximité du flan gauche du portique, là où se situe le fin de course du chariot laser ; lors d’une remise à 0 (le chariot laser et le portique se déplacent jusqu’à rencontrer les fins de course), le couple de maintien des moteurs pas à pas est faible, et ne suffit pas à garantir que le chariot ne se redéplace pas un peu après avoir rencontré le fin de course.
Le remède consiste à installer le faisceau dans 2 chaines porte câble ; celà implique de changer les câbles (ce qui est particulièrement compliqué, car les petits connecteurs sont presque tous différents et pour certains très difficiles à trouver), ou de les rallonger, ce qui exige une bonne préparation ; attention, pour ce faire, il faut que les maillons des chaines puissent s’ouvrir (la section des connecteurs est trop importante pour passer dans la chaine), ce qui n’est pas le cas des chaines que j’ai approvisionnées ! j’ai contourné ce manque en fendant sur le bas quelques maillons parmis ceux qui ne bougent pas lors des mouvements de la machine.
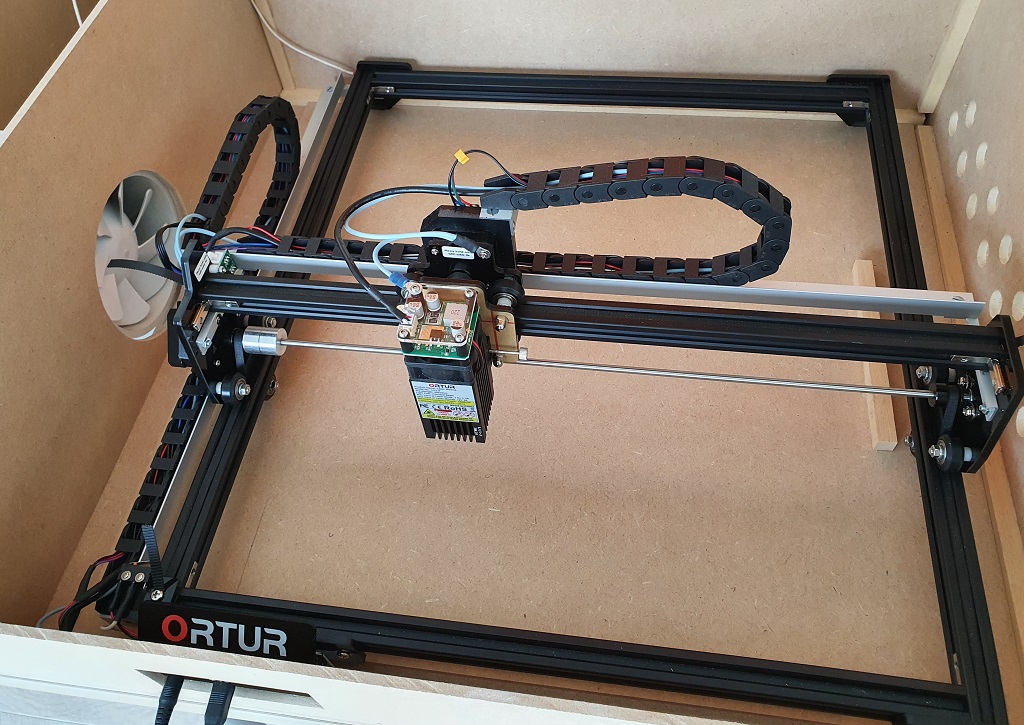
2 - Conception du futur panel :
Le panel est un empilement de 3 éléments :
– La face avant, qui porte les diverses inscriptions blanches, et qui doit être rétroéclairable ; le principal chalenge est d’avoir des inscriptions précises et bien blanches sans le rétroéclairage, et un rétroéclairage uniforme, sans zone de surbrillance.
Elle est constituée de PMMA opale (transparence 40%) de 6, recouvert de peinture blanche puis de peinture grise ; elle est ensuite gravée, ici au laser, en faisant en sorte que la couche blanche ne soit pas attaquée (c’est bien là le sujet !).
La face avant est fixée sur la contre-face.
– La contre-face, qui permet de fixer le panel sur ses rails, porte les composants volumineux qui ne peuvent être directement montés sur le PCB (typiquement les switchs, potentiomètres, et autres encodeurs).
Elle est constituée de PMMA transparent de 10, avec au-dessus les lamages permettant d’y intégrer les écrous des composants, et en dessous une poche (un évidement) qui permettra d’y loger le PCB. Des lamages arrières latéraux de 6 de permettent de réduire l’épaisseur du panel au dessus des rails de fixation (6 mm pour la face avant, et 4 mm pour la contre-face).
– Le PCB, encastré à l’arrière de la contre-face, qui porte les autres composants, switch push-button, connecteurs, led et résistances pour le rétro-éclairage.
J’ai choisi de monter les leds du rétro-éclairage sur ce pcb (plutôt que sur un pcb intégré dans la face avant, de façon à réduire la complexité de l’ensemble (un seul pcb), et surtout pour éloigner les leds du dessus de la face avant ; en effet, leur angle d’ouverture est typiquement de 120°, et la zone éclairée est bien moins importante si la led est placée à environ 3,5 mm du dessus de la face avant (intégration du pcb dans la face avant), ou 10 mm plus loin (intégration du pcb à l’arrière de la contre-face) ; il en résulte un nombre nécessaire de led bien moins important.
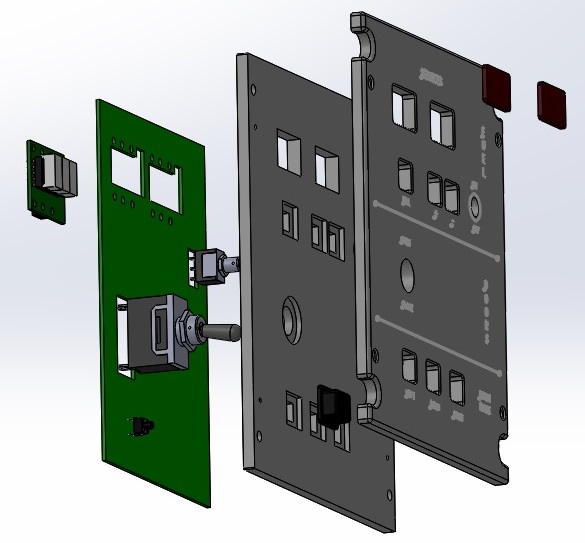
Conception de l’ensemble sous Solidworks, et avec Kicad pour le PCB ; il s’avère que l’utilisation d’une CAO plus orientée 2d est plus pratique, j’ai au final tout repris sous Turbocad.
3 - Réalisation de la face avant :
La face avant est usinée à la CNC, fraise de 3, 1 dent : le PMMA est perçu comme délicat à usiner (fonte du plexi), il faut adopter de bons paramètres, dans ce cas 8000 tours/mn, avance 1200 mm/mn, soufflage à l’air comprimé.
Congés de 1,5 de rayon pour les contours du panel, chanfrein de 1 de profondeur pour certaines des ouvertures, tous 2 réalisés avec une fraise hémisphérique de diamètre 3, CAMBAN (le logiciel qui permet de définir les usinages sur la base d’un fichier .dxf issu de CAO) permet de faire celà facilement ; la profondeur de passe pour les congés est de 2/10, et 1/10 pour les chanfreins.
Avant peinture (à la bombe), la face avant est poncée finement, grain 180 puis 500 ; 2 couches de peinture blanche – 2 passages croisés à chaque fois, séchage puis 2 couches de peinture grise. Attention, la peinture blanche est une peinture spéciale, dite “blanc électroménager”, il s’agit d’une laque émaillée – ceci est essentiel pour la réussite de la gravure laser diode; la peinture grise est une peinture auto.
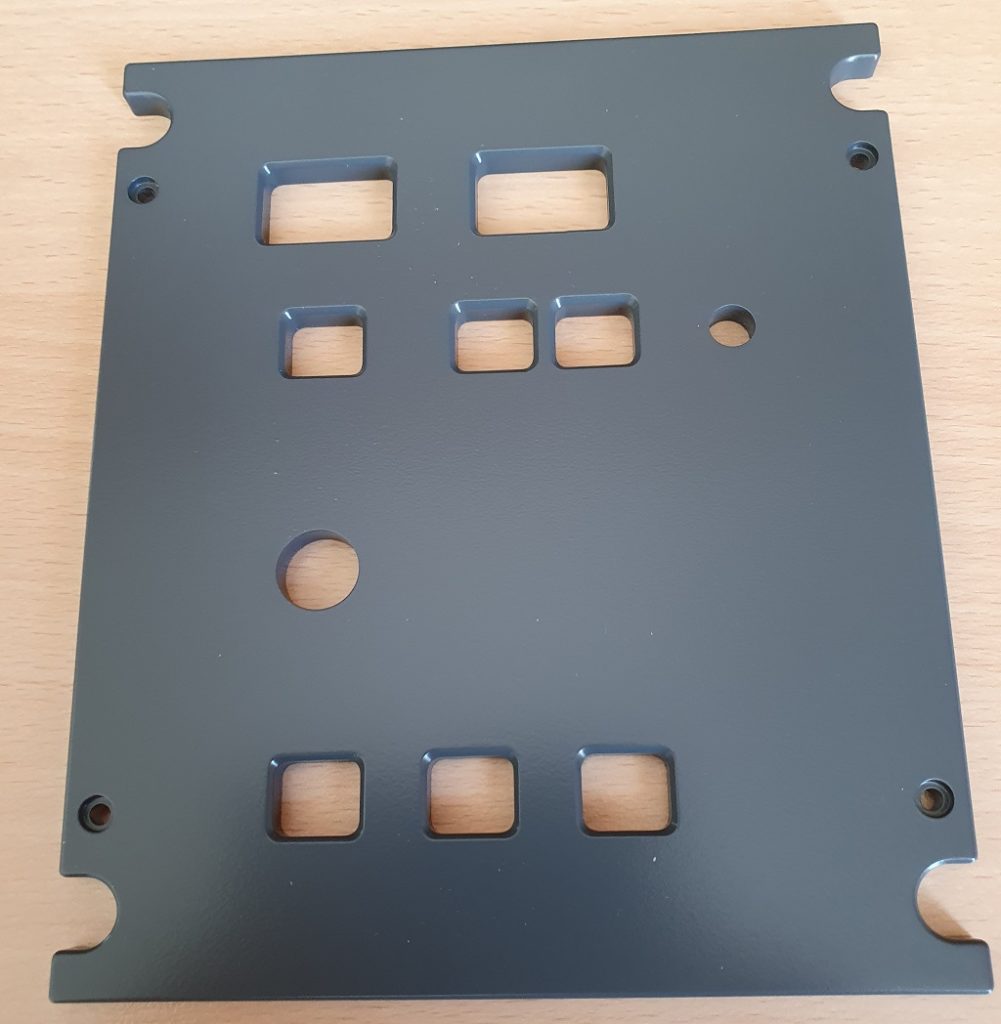
Le dessin de la gravure est préparé sous Turbocad (les diverses lignes ou cercles), le fichier dxf ensuite exporté vers Lightburn comporte également le positionnement des ouvertures ainsi que le contour du panel. Les diverses inscriptions lettrées sont rajoutées directement sous Lightburn (l’import dxf de Lightburn n’accepte que des éléments simples, les courbes complexes et les lettrages ne sont pas acceptés).
La gravure permet de finaliser, en reprenant les principes de positionnement et de paramétrage évoqués précédement.
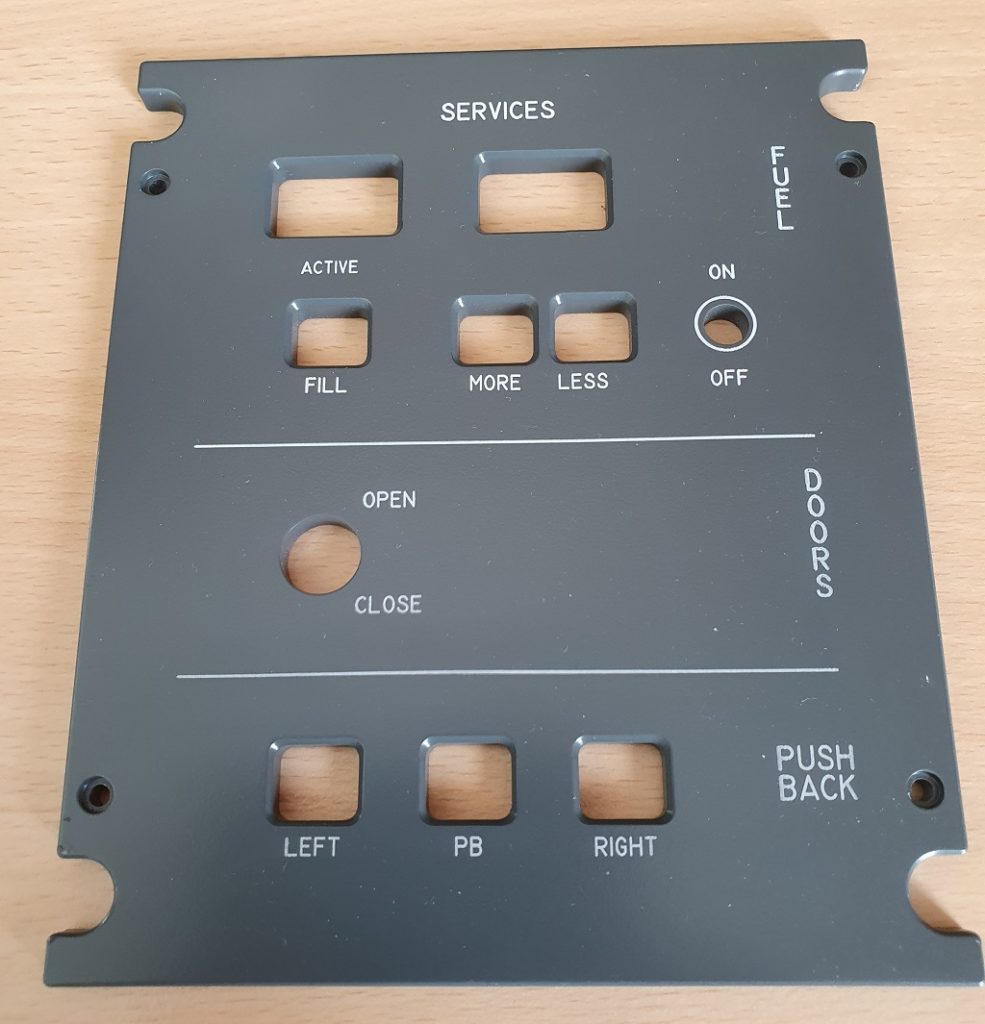
4 - Réalisation de la contre-face :
La contre-face est également usinée à la CNC, fraise de 4, 1 dent ; au recto, ouvertures pour les composants traversant, lamages de 2.2 pour les écrous des composants vissés (leurs écrous ont en général une épaisseur de 2), et contour ; au verso, poche de 4 pour les leds, et lamage périphérique de 1,6 sur 1 de coté pour le pcb ; ne pas oublier quelques plots pour la fixation du pcb ; il convient également de réaliser les lamages latéraux pour fixation sur le cadre d’accueil du panel.
Pour la reprise au verso, je commence par pratiquer une poche de 3 à 4 dans un martyr en mdf, contour plus grand que le contour de la pièce à reprendre (contour légèrement agrandi tout autour, plus 2/10), et dont l’origine coïncide avec celle de la pièce ; puis, sans libérer le martyr et sans arrêter la machine (donc sans perdre la position XY de la broche), encastrement et ablocage de la pièce à reprendre, et lancement de l’usinage ; la précision d’un tel procédé est de 2 à 3/100.
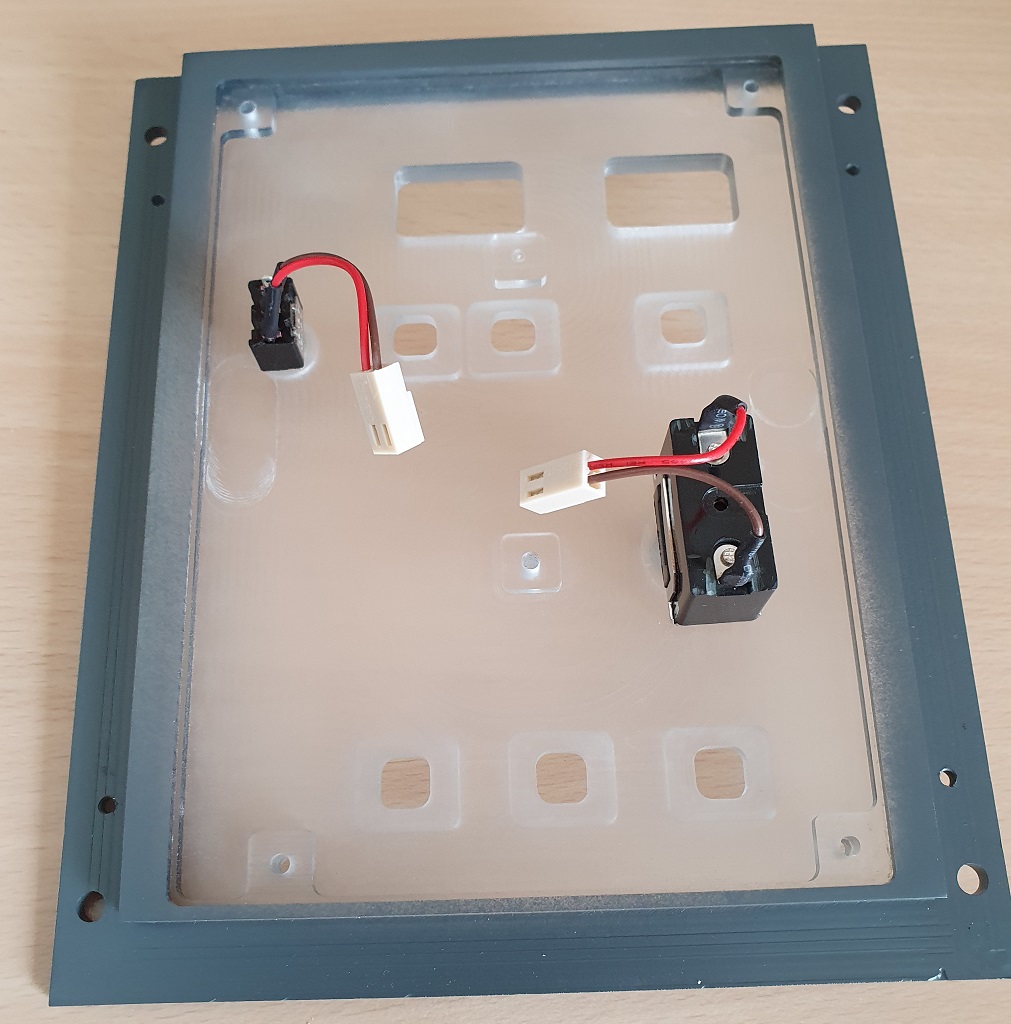
Pour finaliser, peinture grise : au recto, une bande de l’ordre d’une quinzaine de mm (masquage au ruban de masquage) tout autour, et au verso, toute la surface la plus arrière (je découpe une pièce de mdf de la taille du pcb, mois 5/10 tout autour, que je place dans le lamage du pcb, cela fait office de cache).
5 - Réalisation du PCB :
C’est un exercice de style : réalisation au laser !
– La réalisation du dessin du masque de gravure est un peu lourde :
Le dessin du contour du pcb, des ouvertures, ainsi que la place des composants dont la place est imposée, est réalisé sous Turbocad ; pour le positionnement des leds cms au format 3528 (dimension 3.5 x 2.8 x 1.9), j’utilise une forme rectangulaire de 3.5 x 2.8 entourée d’un cercle matérialisant la zone d’éclairage direct de la led ; la dimension du cercle est fonction de l’angle d’ouverture de la led et de la distance surface led à surface panel, en l’occurence environ 16 mm ; le jeu consiste à positionner un certain nombre de ces formes de façon à ce que toutes les inscriptions soient illuminées, sans que les led ne soient directement dessous.
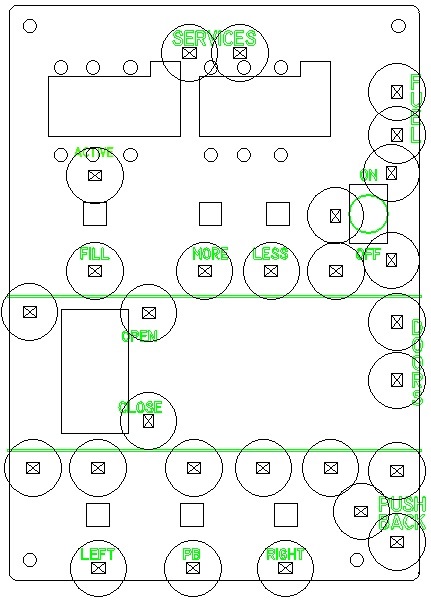
Le fichier résultant est importé au format dxf sous Kicad.
Le dessin du schéma et du tracé recto et verso est réalisé sous Kicad ; j’ai créé un jeu d’empreintes spécifiques dérivées des empreintes de base en agrandissant légèrement la taille des pastilles et en diminuant la taille des perçages afin de tenir compte du diamètre du faisceau laser ; le positionnement des empreintes est réalisé sur la base de l’import dxf, il doit être particulièrement précis pour les composants traversants (type switch push-button).
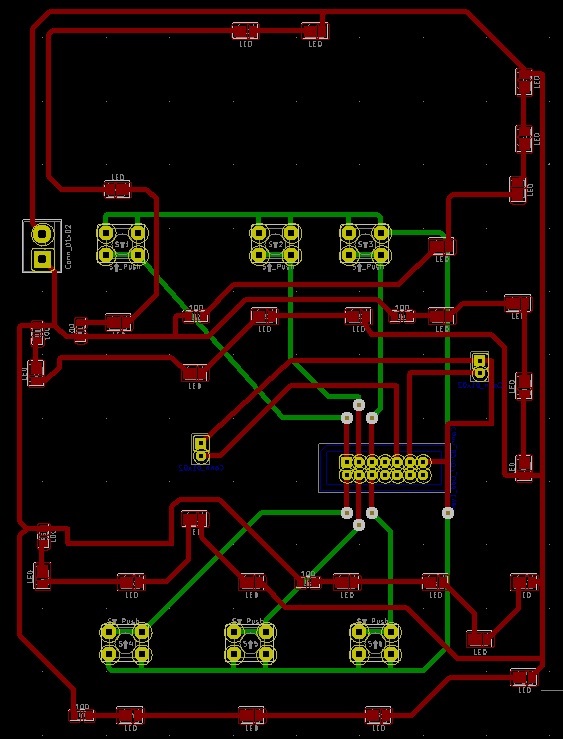
Les plans de masse et autres surfaces cuivrées ne peuvent être réalisés sous Kicad, car Lightburn ne les reconnaitra pas (reconnaissance dxf sommaire) ; il faut donc exporter les dessins recto et verso du pcb (sans oublier la trace des percages) au format dxf vers Turbocad pour les rajouter en n’utilisant que des formes simples (segments, polylines).
– Une fois cette longue phase de dessin terminée, il faut découper le contour et les ouvertures du pcb (CNC), puis, après nettoyage méticuleux, peindre les 2 faces.
– La gravure laser est réalisée selon les paramètres évoqués plus haut ; la difficulté réside évidement dans le positionnement recto-verso : il faut donc réaliser les 2 gravures en utilisant la méthode du cadre (voir ci-dessus), avec la meilleure des précisions possible (au moins 1/10), et en ayant assuré au mieux l’orthogonalité XY de la graveuse.
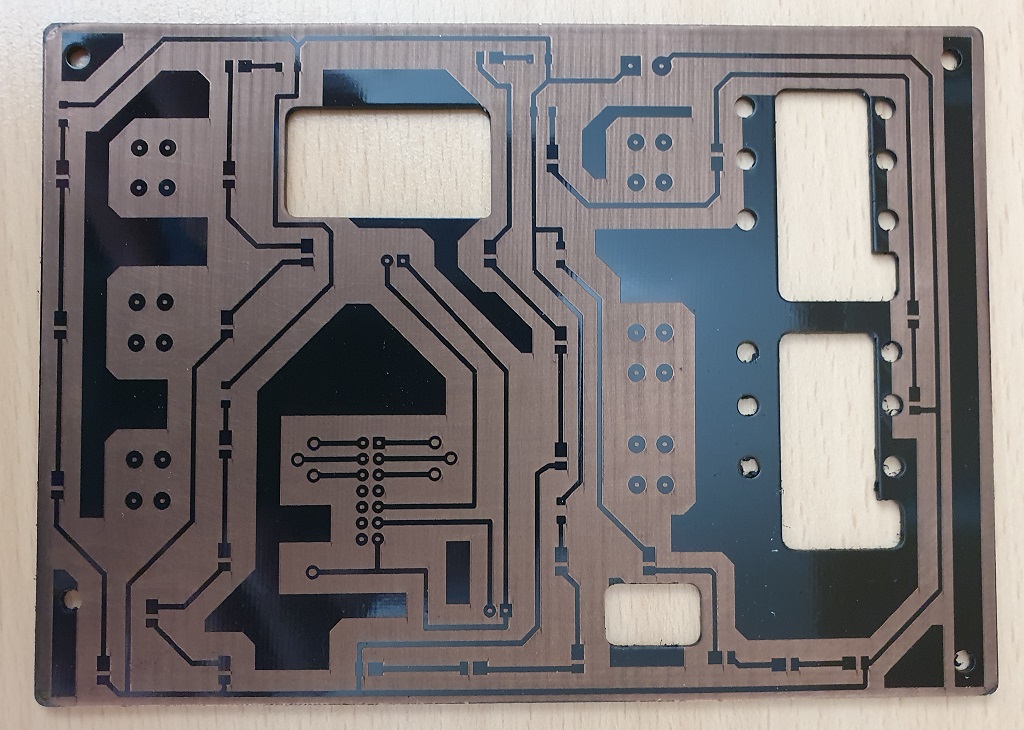
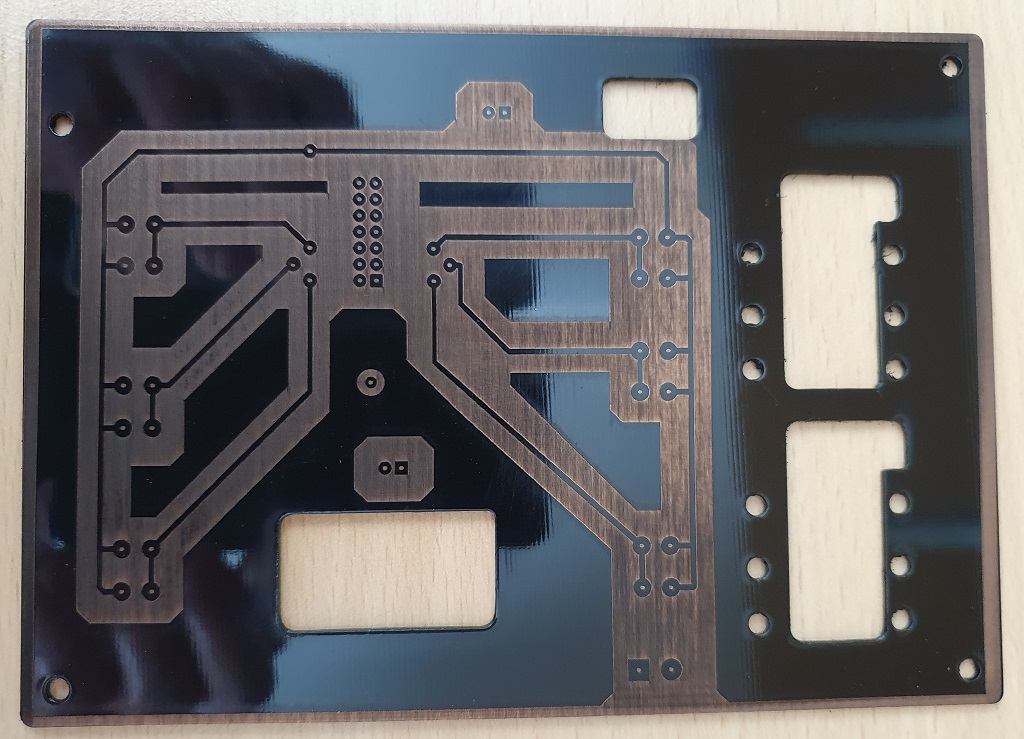
– Vient ensuite l’opération de gravure chimique, je plonge simplement le pcb dans le mélange et l’agite tranquillement (gant de chirurgien) ; résultat parfait, nettoyage à l’acétone.
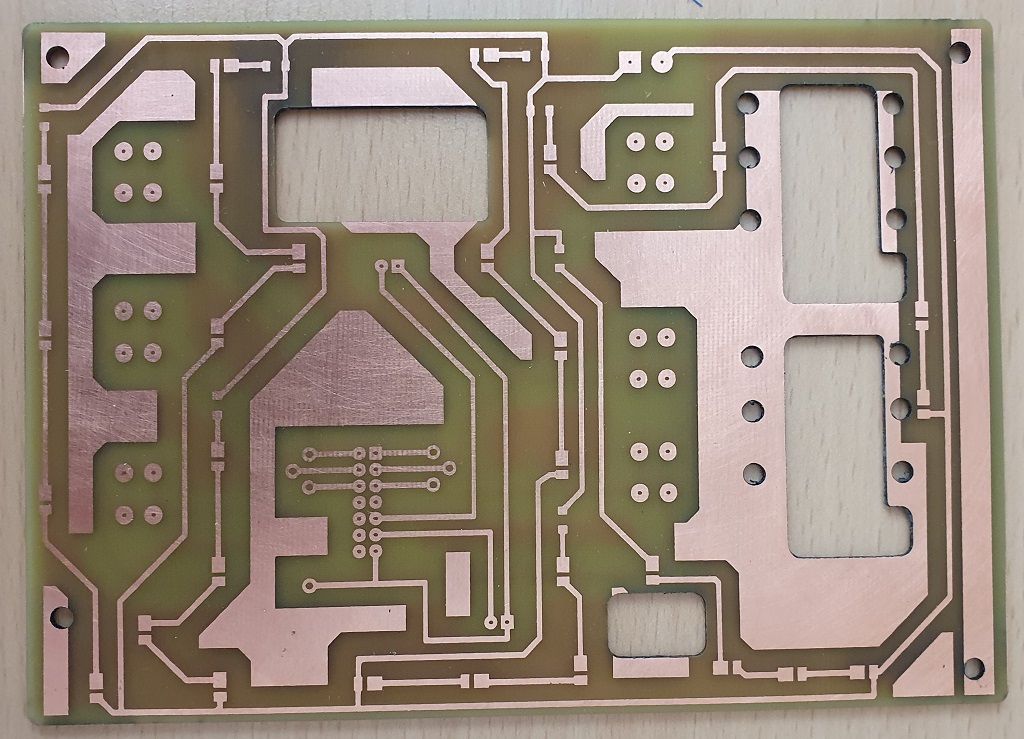
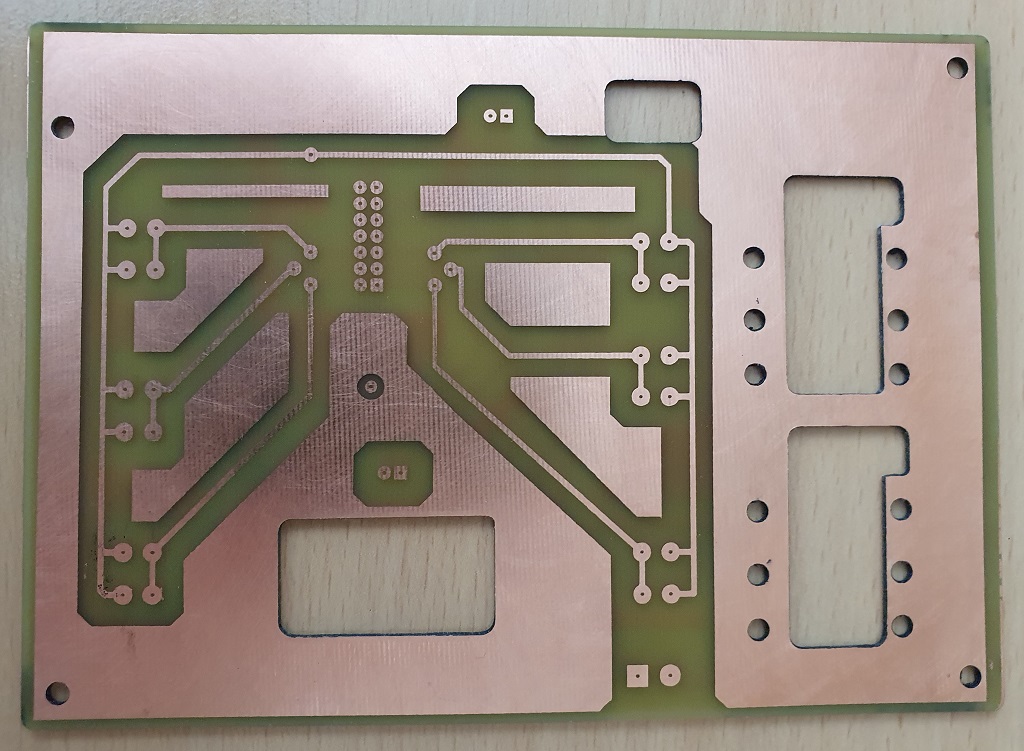
– L’étape de vérité arrive : pour savoir si le résultat est satisfaisant (correspondance recto-verso), il faut procéder aux perçages : petite perceuse sensitive, forets de 0.8 et 1, l’opération est d’autant plus précise que la taille des perçages des empreintes des composants a bien été ajustée. Le perçage des jonctions recto-verso doit être correctement centré des 2 cotés, et – gros soulagement – c’est bien le cas !
– Pour finaliser, léger ponçage (grain 500) puis étamage liquide, ceci afin de protéger le circuit et faciliter les opérations de soudure.
– Enfin, opération soudure, en commençant par les plus petits composants : les résistances cms (format 1206, dimension 3.2 x 1.6 x 0.55), ainsi que les leds au format 3528 ; c’est un peu petit, j’utilise un fer à souder à pointe fine, de la soudure diamètre 0,5 : je positionne le composant à l’aide de bruxelles, place dessus un poids lourd en laissant libre l’un des cotés à souder (j’utilise une équerre à semelle en acier), coupe un tout petit tronçon de soudure (2 mm) que je pousse contre le coté à souder, pose la panne du fer sur la pastille de cuivre et viens au contact de la soudure ; la soudure est quasi instantanée, je retire le fer, il n’y a plus qu’à souder l’autre coté.
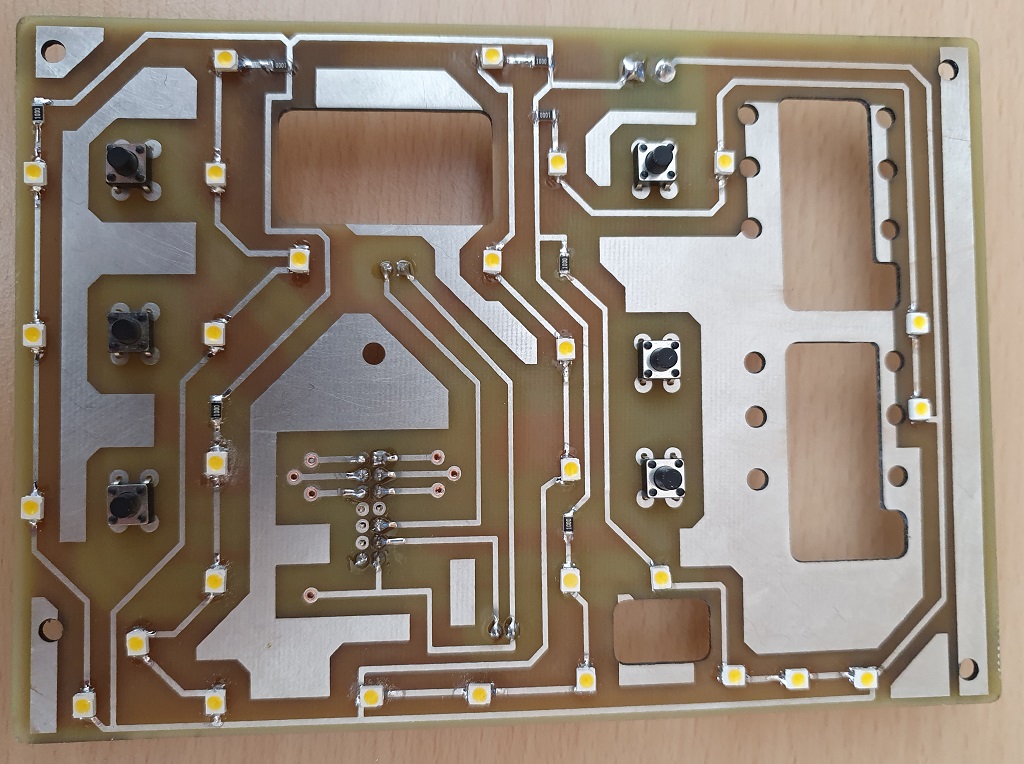
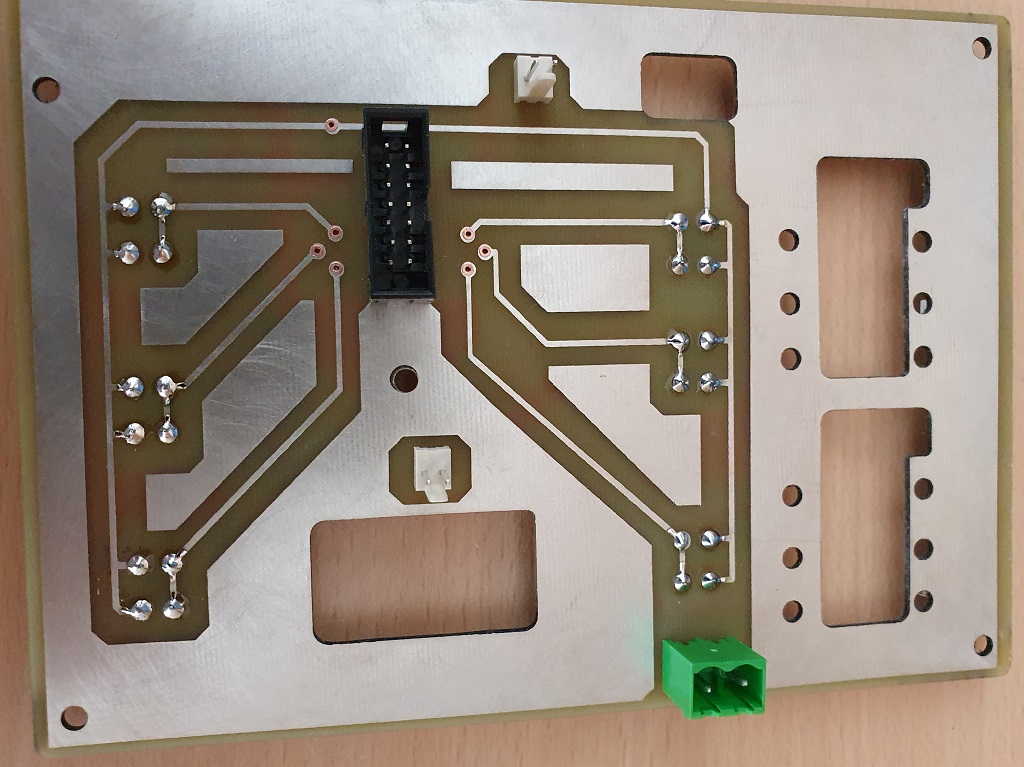
Pour assurer les liaisons entre faces, j’utilise des vias de 1 mm de diamètre ; pour le sertissage, j’ai tourné un petit outil dans du stub de 6 , petite “pointe” de 1,5 de long, diamètre 75/100 (le diamètre interne des vias est de 8/10).
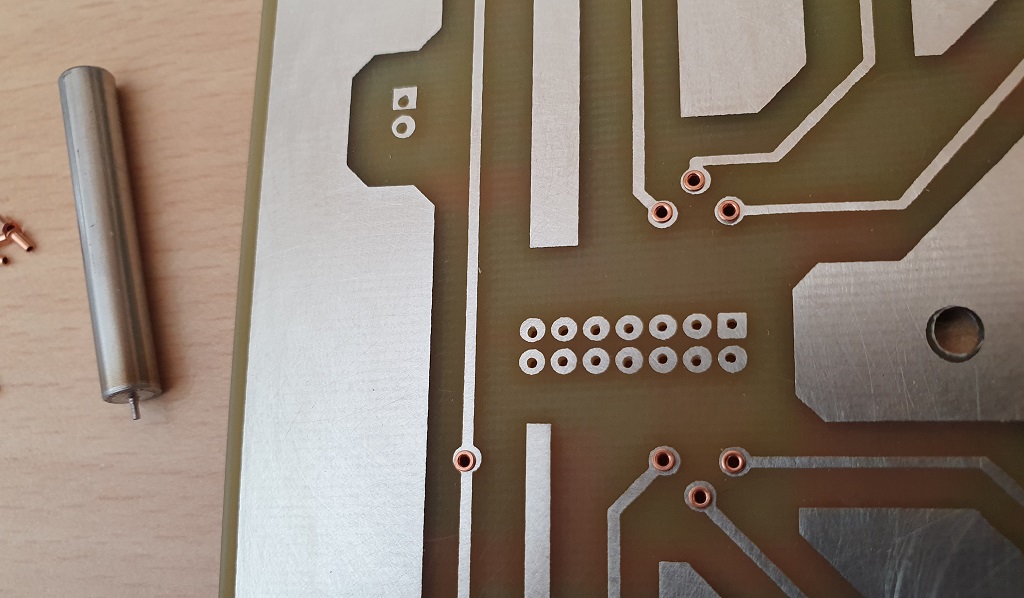
6 - Le panel terminé :
Il reste quelques petites opérations à réaliser pour terminer :
– montage des gros composants (switchs) sur la contre-face et cablage avec un petit connecteur 2 points pour connexion sur le pcb,
– fraisage des poussoirs pour les push-button : ils ne sont pas rétro-éclairés, donc j’utilise simplement du polycarbonate noir,
– préparation des vis de fixation de la face avant sur la contre-face : visserie m3, je travaille un peu les têtes au tour avec une petite lime et à l’abrasif grain fin pour les bomber, puis peinture à la bombe grise, en laissant le filetage intact.
Et montage final : le résultat est à l’arrivée, les gravures sont bien blanches,
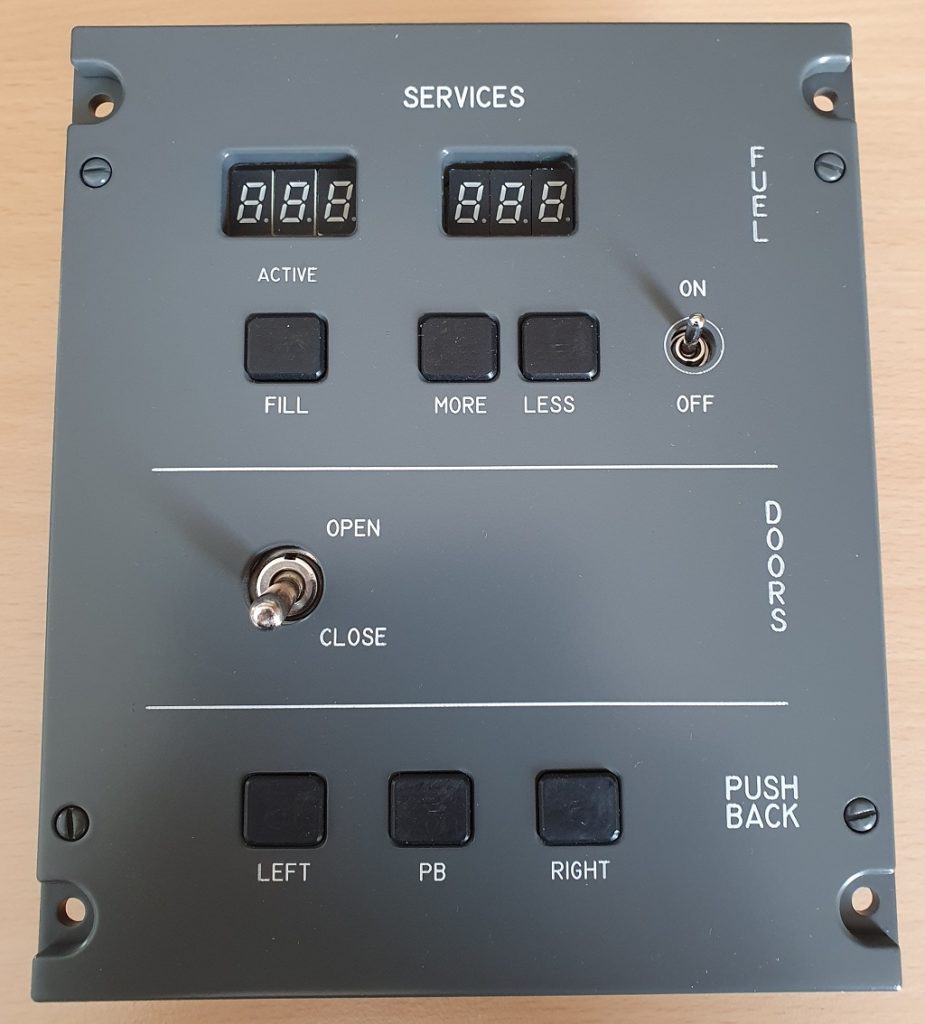

présentation en place, le rétro-éclairage est bien homogène, pas de point de sur-brillance, mission accomplie !

Il ne reste plus qu’à programmer tout cela (SIOC), mais c’est une autre histoire …
En tous les cas, ce genre de petite graveuse s’avère un incontournable pour qui veut réaliser ses panels, tant il simplifie les opérations de gravure qu’il fallait conduire à la CNC.
Bonjour,
Je suis très intéressé par votre sujet.
Serait-il possible d’voir une description détaillée de la façon dont vous passez du circuit Kicad au fichier utilisable par votre graveuse Laser (LaserGRBL) ?
Merci
Cordialement
Bonjour Philippe,
Dans KiCad, j’exporte les 3 couches F.Cu, B.Cu et Edge.cuts au format .dxf.
Je reprnds ensuite ces 3 fichiers dans une CAO/DAO capable de traiter les .dxf, en l’occurence Turbocad :
chargement de B.Cu et superposition de Edge.Cuts ; idem avec F.Cu.
Sur les 2 fichiers obtenus, je rajoute ensuite les réserves, retire les éventuelles ouvertures, et rajoute un cadre +0.1 mm tout autour, future limite de la gravure ; il s’agit d’obtenir les 2 fichiers finaux de gravure.
Finalement, import dans LightBurn et paramétrage des opérations de gravure.
Nb : avant ces opérations, je prépare un .dxf contenant le contour du PCB, les ouvertures, le placement des composants dont le positionnement est imposé, … ; c’est ce fichier que j’importe ensuite dans KiCad-PcbNew dans une couche autre que Edge.cuts, c’est ce qui va me servir ensuite de repère pour toutes les opérations de placement.
Michel
Bonjour,
Je suis très impressionné par votre travail.
Est ce que vous avez modélisé vous même la gravure laser ? Si oui dans le logiciel de la découpe laser ou plutôt sur solide works ou fusion 360 ?
Merci beaucoup
Bonjour,
le dessin de la gravure peut être réalisé dans Lightburn (le logiciel de gravure), mais les fonctionalités du logiciel sont tout de même un peu pauvres ; nul besoin d’une CAO 3D comme SW ou Fusion, une CAO 2D est suffisante, il s’agit simplement de pouvoir produire un résultat au format dxf ; pour ma part, tous les dessins de panels sont réalisés sous Turbocad.
Michel
Bonjour,
super merci pour votre réponse.
Est ce que ça ne vous dérange pas de me transferer les fichiers DXF ?
Merci beaucoup d’avance
Eliott
Bonjour Eliott,
Je suis désolé de répondre par la négative : j’ai par le passé souvent répondu positivement, cela ne m’a valu que des ennuis.
En l’occurence, les panels dont il s’agit sont des panels spécifiques, derrière la gravure il faut les fichiers de réalisation du panel, puis le schéma électrique et le dessin du PCB, puis le programme pour l’animer, etc … je ne suis plus prêt à assumer le suivi de tout celà.
Celà étant, disposer de l’outil de CAO reste à peu près indispensable pour se lancer dans ces réalisations, et dès lors le dessin de la gravure est certainement l’opération la plus simple à réaliser !
Michel
Bonjour,
Je comprends tout a fait.
Merci beaucoup du conseil !
Eliott