Dans le précédent volet de ce sujet, je vous ai montré 3 formules pour rétro-éclairer les panels (pour mémoire, un panel, c’est une face avant en PMMA blanc un peu translucide, épaisseur d’environ 6 mm, peinte et gravée, et une contre-face, épaisseur de l’ordre de 3 mm, sur-laquelle sont montés les divers switchs, potentiomètres, commutateurs, korrys, afficheurs, … :
– Version 1 : des bandes de leds sont positionnées en face arrière du panel ; solution simple mais insatisfaisante, la diffusion de la lumière vers la face avant est gênée par le câblage du panel, ce qui altère l’uniformité de l’éclairage.
– Version 2 : des leds cms sont soudées sur un pcb lui-même positionné derrière la contre-face ; le résultat est tout à fait satisfaisant sauf là où un composant volumineux occulte certaines gravures ; la solution est moyennement simple, le positionnement des leds est assez délicat, et leur nombre est nécessairement important car leur angle de diffusion n’est que de 120°.
L’inconvénient de cette formule, outre le problème des gros composants (par exemple les push-pulls du FCU), est que l’éclairage n’est pas intégré dans la face avant, ce qui peut gêner le câblage, et altère la maintenabilité.
– Version 3 : des micro-bulbes à incandescence (hauteur 3,5 mm, très difficile à trouver) sont soudés sur un pcb lui-même encastré dans la face avant ; cette formule, qui exige un travail particulièrement délicat de la face avant, procure un excellent résultat, et est conforme à la norme MIL-P-7788 illuminated panel – type V, qui régissait la grande majorité des panels aviation.
L’inconvénient de cette formule réside dans la grande complexité de la mise en oeuvre, et, pour un amateur, sa faible répétabilité.
Il faut également souligner que la consommation électrique d’un panel ainsi traité est importante, et donc accompagnée d’une forte dissipation de chaleur.
– Version 4 : j’ai terminé en présentant une expérience interpellante d’éclairage par la tranche.
1 - Nouvelles perspectives :
Dans l’hypothèse d’une évolution majeure de mon simu, je suis toujours à la recherche d’une solution à la fois très proche de la réalité en terme de résultat, et qui soit, comme dans la réalité, totalement intégrée dans la face avant des panels (épaisseur 6 mm max).
A ce stade, 2 pistes :
– Version 2 bis : on reprend la formule de la version 2 – leds cms soudées sur un pcb derrière la contre-face du panel, mais cette fois-ci la pcb est intégré dans la face avant du panel.
L’épaisseur du pcb est de 16/10, celle d’une led smd 3528 (3,5 mm x 2,8 mm, ça reste facilement soudable) de l’ordre du mm, il faut donc évider le dos de la face avant d’environ 3 mm.
Compte tenu de l’angle de diffusion d’une led cms, environ 120°, et de la distance de la led à la surface de la face avant, il faut que toute gravure à éclairer soit à moins de 8 à 10 mm d’une led.
Par ailleurs, il ne faut pas qu’une led soit directement placée sous une gravure, pour éviter les points de sur-brillance.
Tout ceci débouche sur une forte densité d’implantation des leds : pour exemple, un lights panel d’A320 (326×132) exige plus de 100 leds, et plus de 30 résistances (1 résistance par groupe de 3 leds pour une alimentation sous 12V).
Cette formule correspond au tout dernier niveau de la norme MIL-P-7788 – type VII, devenu le standard.
La principale difficulté de cette formule réside dans la réalisation du pcb, et la soudure d’une multitude de leds et résistances cms.
L’apparition d’acteurs asiatiques offrant la réalisation de pcbs et même leur assemblage à des tarifs extrêmement agressifs permet d’envisager cette formule, il faut juste concevoir les pcbs à l’aide d’un soft délivrant des fichiers Gerber ; il n’en reste pas moins que pour un gros panel, le travail de conception est important.
– Version 4 bis : il s’agit là de poursuivre dans la voie expérimentée en version 4, celle de l’éclairage latéral, désormais très utilisé pour le rétro-éclairage des écrans TV ; c’est l’apparition de leds smd à éclairage latéral, et de bandes de leds ainsi équipées, qui m’ont décidé à poursuivre dans cette voie, que je vais développer ci-avant.
2 - Rétro-éclairage latéral :
2.1 - Principes :
Il s’agit de placer un guide de lumière juste sous les gravures à éclairer ; sur les bords du guide, des bandes de leds, et entre le guide et les gravures, un dispositif qui capte la lumière émise par les leds et la dirige vers les gravures.
Un guide de lumière met à profit les lois de la physique relative à la propagation des rayons lumineux entre 2 milieux.
Nous considérons un rayon lumineux qui navigue dans une plaque de PMMA transparent (émis par une led placée contre sa tranche) ; selon son incidence par rapport à la surface de la plaque, il va se réfléchir et rester à l’intérieur, ou se réfracter vers l’extérieur ; l’angle limite, dit “critique” (angle entre le rayon et la perpendiculaire à la surface au point de “contact”) est, pour une plaque en PMMA et de l’air à l’extérieur, d’environ 42°.
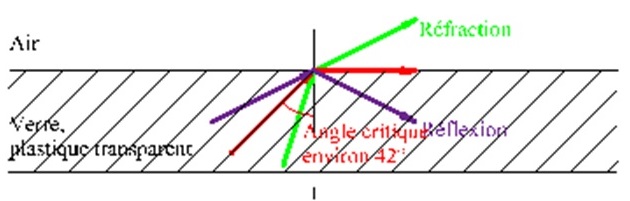
Certains rayons vont, de réflexion en réflexion, se propager dans la plaque, alors que d’autres vont se réfracter dès leur émission vers le haut ou vers le bas.
Si l’on peint en blanc la surface inférieure de la plaque, les rayons qui se seraient diffractés vers le bas vont être aussitôt réfléchis vers l’intérieur selon un angle égal à l’angle d’attaque, et donc se réfracter au contact de la surface supérieure. Nous voilà donc avec les rayons restant qui s’apprêtent à traverser la plaque et ressortir à son extrémité opposée, pas très intéressant pour le rétro-éclairage !
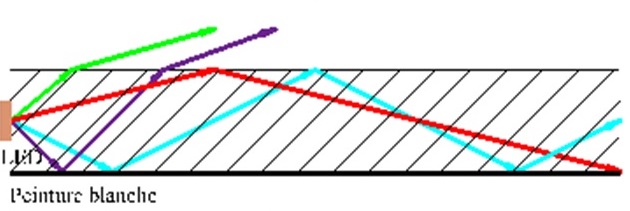
Supposons un rayure aux flans formant un angle aigu à la surface de la face supérieure : un rayon intérieur qui se serait réfléchi va attaquer le flan sous un angle tel qu’il va être diffracté vers le haut.
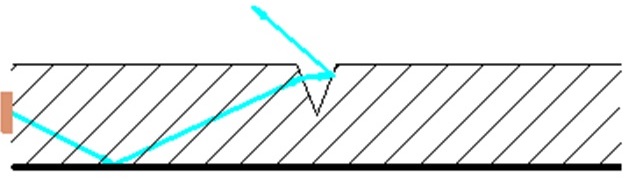
Nous avons donc tout ce qu’il faut pour faire voyager la lumière dans une plaque de PMMA et la faire émerger vers le haut au fur et à mesure de sa progression : pour cela, on grave de fines rayures sur toute la surface supérieure de la plaque, et l’on dispose de chaque coté de cette plaque des bandes de leds (dont je rappelle qu’elle sont assez directives).
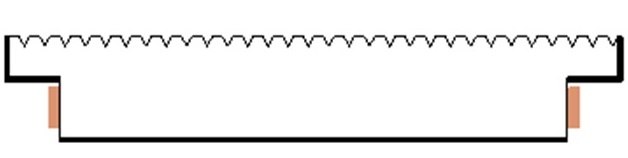
Faisons un pas de plus vers l’application : le guide de lumière est peint en blanc sur sa surface inférieure ; sa surface supérieure est gravée finement – quadrillage oblique, gravure à la fraise javelot 15°, profondeur 2/10, espacement des lignes 2 mm ; au pourtour, un lamage permet d’y positionner des bandes de leds à éclairage latéral ; le tout est encastré dans la face avant, évidée pour ne laisser plus qu’un voile de 2 mm au-dessus et autour.
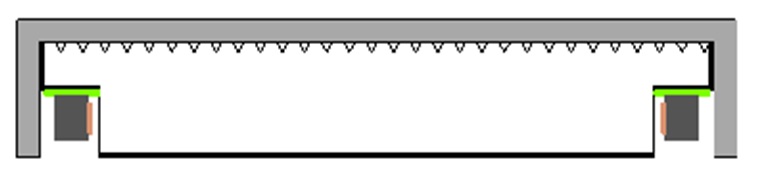
2.2 - Réalisation d'une maquette
Pour la circonstance, je vais utiliser un petit panel fabriqué par l’excellent “HomeCockpits.fr” : face avant PMMA presque blanc, 6mm, peinture bi-composant, gravure laser, et contre-face PMMA tranparent 3 mm.
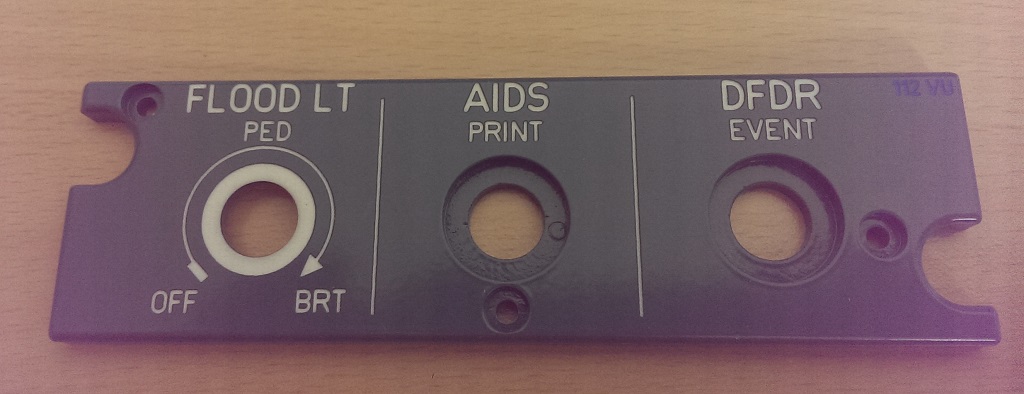
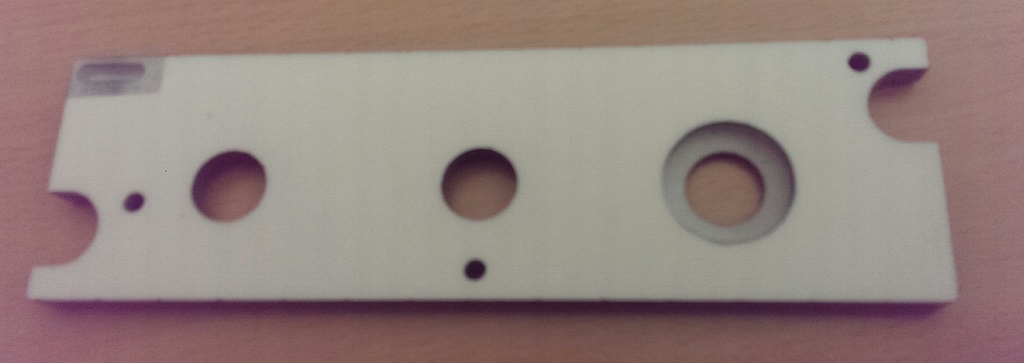
La première étape consiste à évider la face avant sur une profondeur de 4 mm, tout en laissant une fine paroi autour des ouvertures : réalisation à la cnc, fraise 1 dent diamètre 3 ; le panel est fixé sur la martyr de la machine à l’aide de double face, le décollage est délicat car l’épaisseur de matière restante n’est que de 2 mm, Attention, fragile …
Poursuite à la cnc : le guide de lumière est découpé dans une plaque de PMMA coulé transparent, puis retourné pour gravure à la javelot 15° – fixation également au double face. Le guide est suffisamment petit pour que les écarts d’épaisseur ne soient pas trop importants, ce qui évite d’avoir recours au levelling.
Les bandes de leds à éclairage latéral : je n’ai trouvé que des bandes étanches (norme IP65), elles sont recouvertes d’un plastique souple transparent, qu’il faut décoller délicatement ; ce sont des bandes à forte densité d’implantation, 120 leds au mètre, blanc chaud.
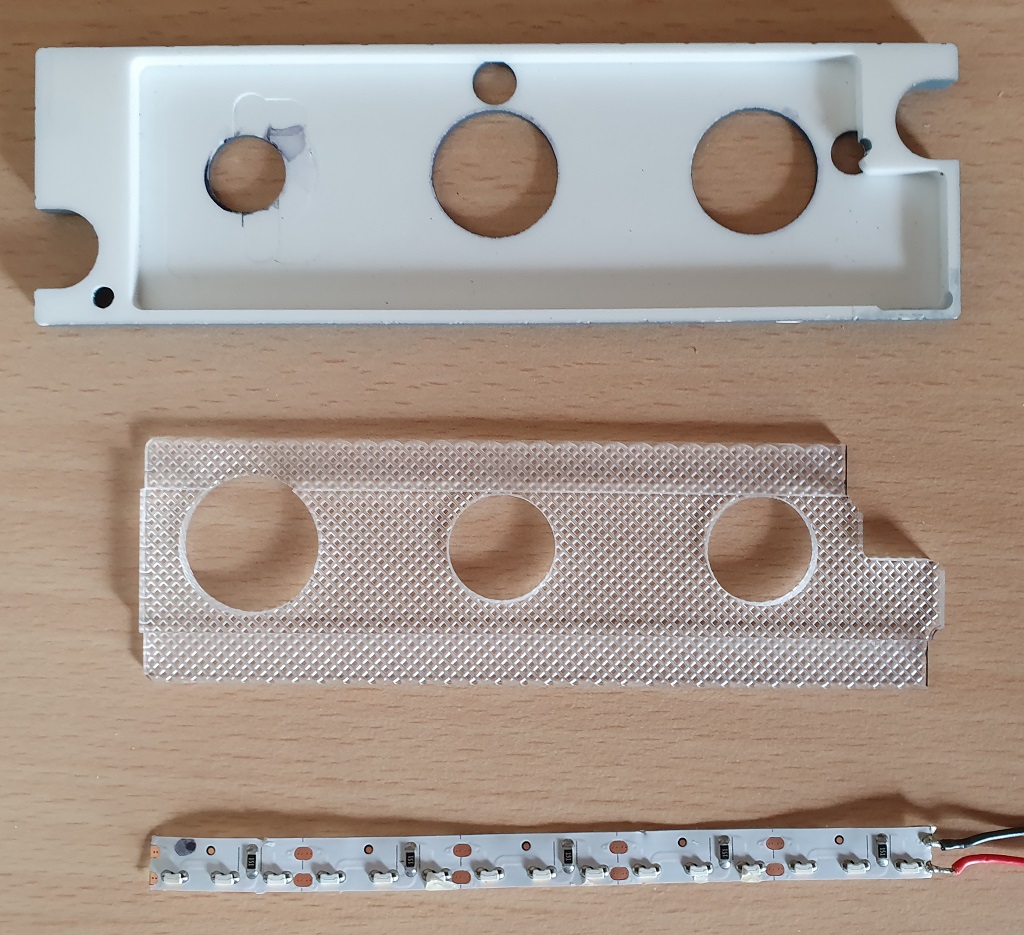
Voici l’intégration des bandes sur le guide, lui même encastré dans la face avant :
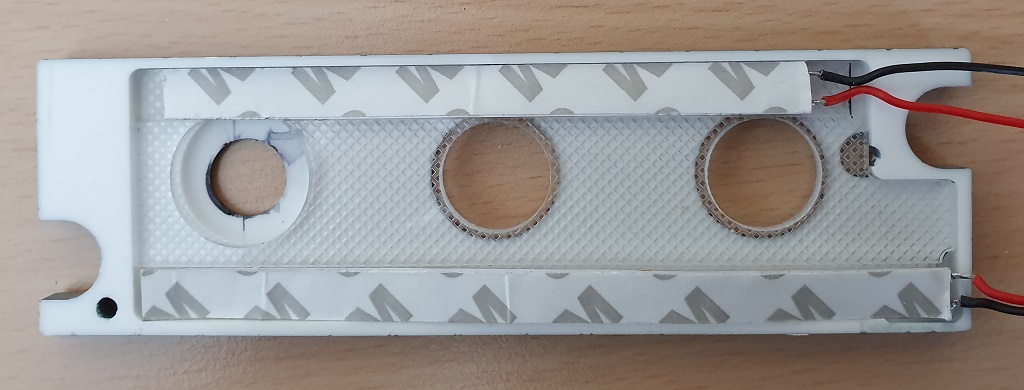
Et enfin, la fixation de la face avant sur la contre-face, équipée pour ce panel de 2 switchs et un potentiomètre. Je n’ai pas encore peint en blanc la face arrière du guide, je vais, pour les essais, intercaler une feuille de papier blanc.
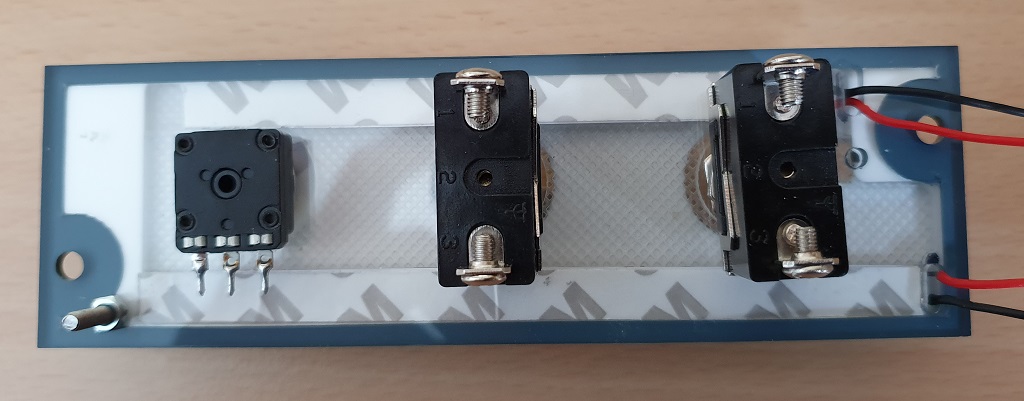
Il ne reste plus qu’à brancher, 12 V CC :
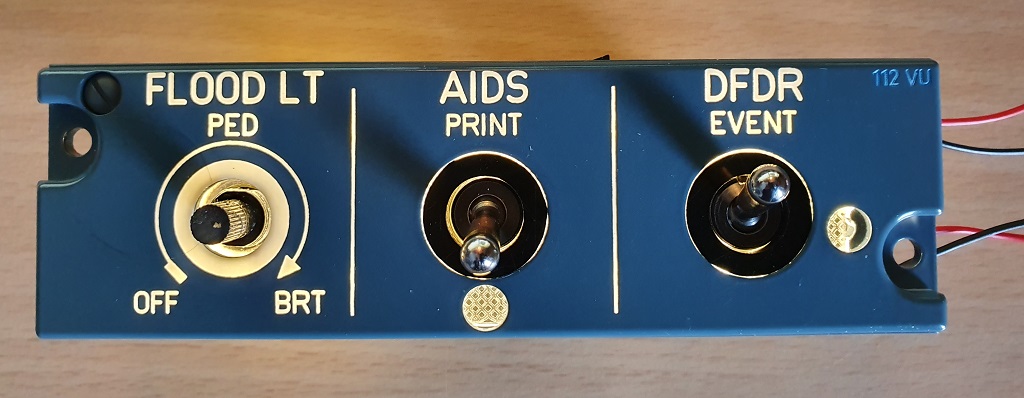
Sur ce petit panel, le résultat est totalement satisfaisant ; mais pour autant, l’affaire n’est pas dans le sac ! ce panel est petit, il ne présente qu’une rangée de switchs et autres korrys ; que se passe-t-il si le panel est doté de plusieurs rangées, qui vont constituer autant d’obstacles à la propagation de la lumière dans le guide ?
2.3 - Et avec un gros panel ?
Pour valider cette formule, je vais choisir l’un des gros panels de l’A320, le “light panel”, situé sur l’over-head, cet ensemble de panels placé au-dessus de la tête des pilotes ; c’est un panel qui mesure 326 x 132, et comporte 15 switchs, 8 korrys et 2 potentiomètres, disposés sur 3 rangées.
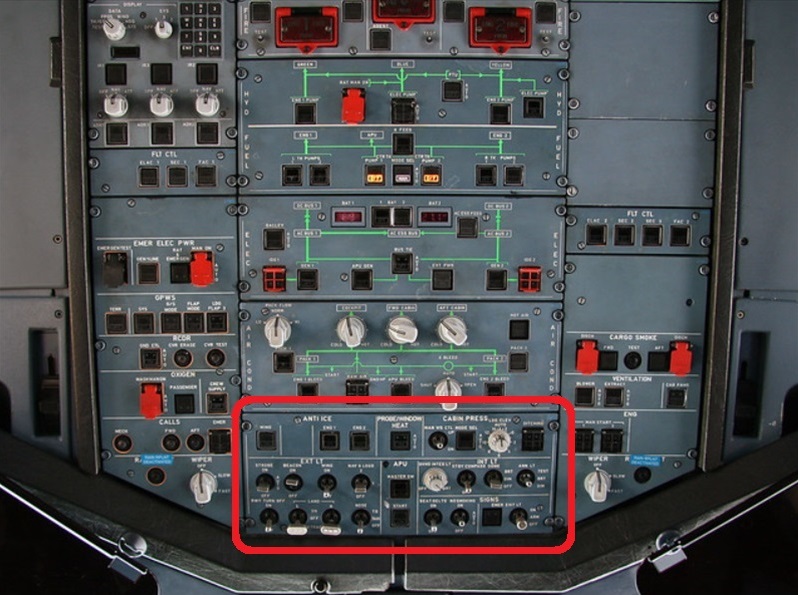
2.3.1 - Réalisation du panel :
Pour la circonstance, je ne dispose pas de panel tout prêt, la première étape, qui ne fait pas partie du test, va donc consister à le réaliser :
– découpe de la face avant et de ses divers ouvertures dans du PMMA 6 mm ; cnc, fraise 1 lèvre diamètre 3 mm, 8000 trs/mn, avance 1400 mm/mn, profondeur de passe 2 mm, as usual …
– peinture de la face avant ; peinture au pistolet, j’utilise de la peinture vinylique mais je sais que ça n’est pas la bonne solution, car cette peinture est élastique, pas très résistante, et ne supporte pas les nettoyants ; mais tellement pratique, à l’eau – il faudrait de la peinture bi-composant, mais là, le nettoyage devient vite une grosse galère …
En tous les cas, tout mon simu est réalisé ainsi ; 4 à 6 couches, séchage au sèche-cheveux entre les couches, c’est l’affaire d’une demi-heure.
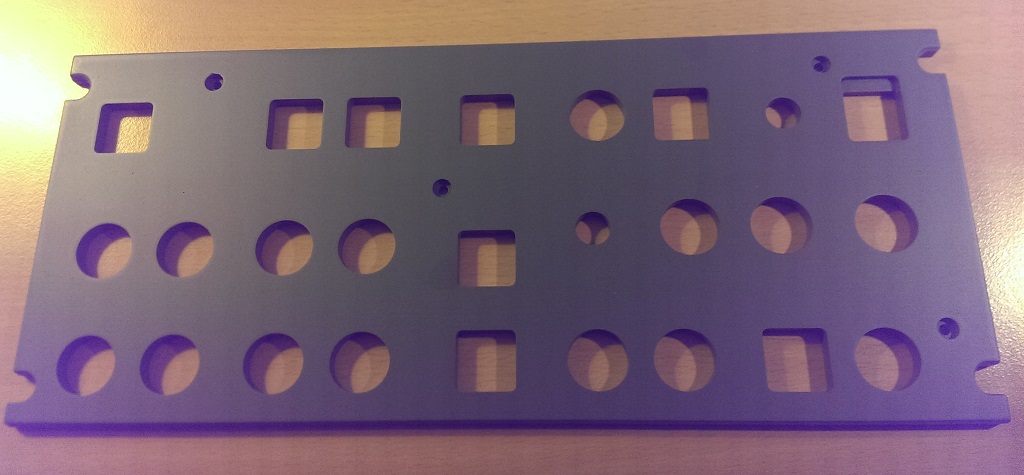
– gravure de la face avant : cette opération est délicate : en effet, il faut graver sur une faible profondeur (10/10 à 15/10), et il est important que cette profondeur soit constante, faute de quoi la largeur des gravures présentera des fluctuations (gravure à la fraise javelot, largeur de gravure fonction de la profondeur).
Or le PMMA (PMMA coulé, par opposition au PMMA extrudé, c’est à dire refondu après polymérisation puis laminé, et qui est plus difficile à usiner – tensions internes, température de ramollissement plus faible) présente des variations d’épaisseur qui peuvent atteindre quelques 1/10 ; en fixant une profondeur de gravure de 15/10, selon l’endroit où l’on a fait le 0, la fraise à certains endroits ne fera que survoler la surface du panel !
La parade réside dans un “leveling” préalable”, qui consiste à effectuer un relevé de niveau, et à répercuter les écarts de hauteur sur la composante Z des ordres du Gcode de gravure : les tracés contenus dans le Gcode sont fractionnés en petits segments de longueur déterminée – par exemple 5 mm – et les Z de leurs extrémités sont corrigés des écarts relevés et interpolés ; un logiciel fait cela, “Autoleveler”, que j’utilise régulièrement, en particulier pour la gravure à l’anglaise des pcbs, et qui donne d’excellent résultats.
Mais là, je rencontre une sévère difficulté imprévue : le relevé proposé par Autoleveler s’effectue selon un maillage dont la maille, paramétrable, est carrée ; et si je paramètre une maille de 8 mm, de nombreux points de sondage se retrouvent dans le vide des multiples ouvertures du panel ; les relevés de ces points seront complètement faux, et les interpolations résultantes parfaitement inexploitables !
En faisant varier la taille de la maille, je finis par trouver qu’avec un pas de 38 mm, seul un point de relevé “tombera” dans un trou – je pourrai le corriger en intervenant dans le fichier des relevés ; mais une maille de 38, c’est à l’évidence beaucoup trop grand … mais faute de mieux, je réalise ce fameux relevé :
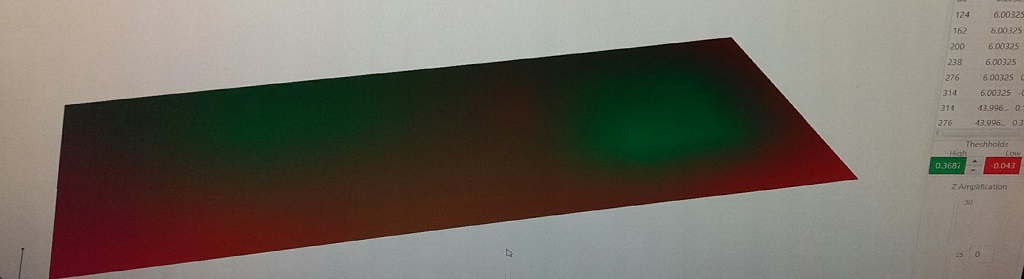
Sur cette image qui représente la surface du panel, les différences de couleur mettent en évidence les écarts de hauteur (en vert les points hauts, en rouge les points bas), l’écart max est proche de 4/10 !!
La gravure s’annonce plus que périlleuse ; et en effet, je suis obligé sur certaines zones de procéder à plusieures opérations de reprise, en augmentant la profondeur de passe par incrément de 5/100 ; résultat déplorable, car de surcroit, j’ai changé de peinture, et cette dernière s’avère élastique, ce qui n’est absolument pas adapté à la gravure …
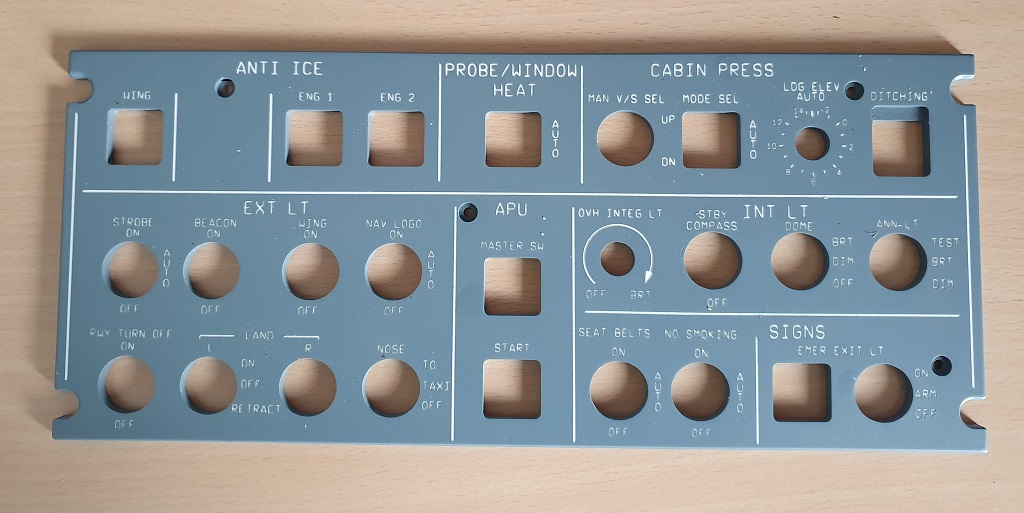
Bon, pour le test de rétro-éclairage, ça n’est pas redhibitoire.
– contre-face : cette dernière est également usinée à la cnc, PMMA transparent 3 mm, puis peinte et équipée, pas de difficulté particulière.
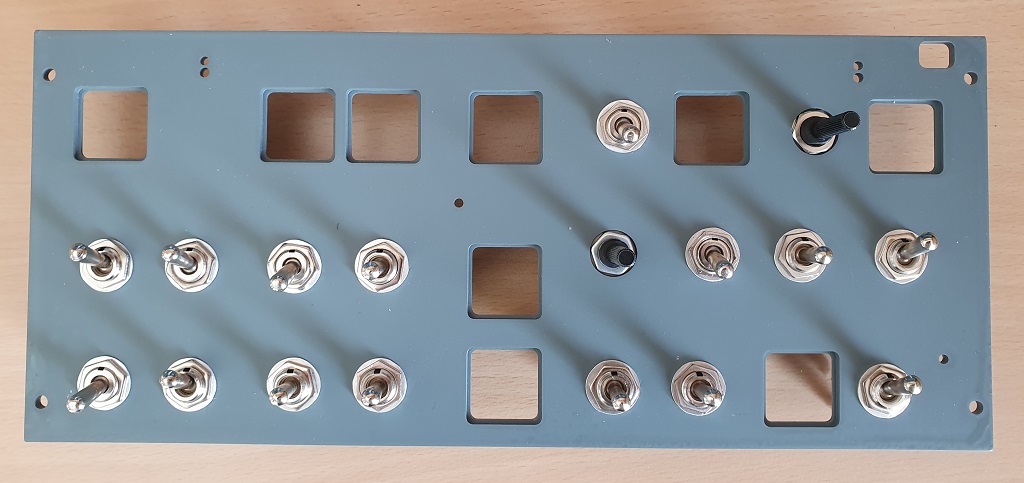
Le panel est prêt pour l’opération rétro-éclairage !
2.3.2 - Rétro-éclairage :
– usinage de la face avant : nous en sommes au même stade qu’au début de la maquette, la première phase va consister à évider le fond de la face avant pour y encastrer le guide de lumière.
Et d’emblée, une nouvelle difficulté se présente, il n’est pas question de fixer la face avant sur le martyr de la CNC à l’aide de double-face : la peinture vinylique ne supportera pas le décollage, et le pannel lui-même risque de se casser, compte tenu de sa faible épaisseur résiduelle et de sa grande taille. Il n’est pas non plus question de fixer la face avant à l’aide de brides, car le bord qui va subsister tout autour du panel ne mesure que 2 mm d’épaisseur ; en outre, le fond du panel ne restera pas plaqué contre le martyr lors du fraisage, du fait de l’effet “tire-bouchon” de la fraise.
Je finis par mettre à profit les ouvertures qui parsèment le panel, et qui resteront toutes bordées par un mince voile de 15/10 destiné à éviter les “fuites” de lumière : j’usine donc des petits bouchons dont la section basse correspond à la taille des ouvertures, et la section haute présente un décalage de 1 mm, qui appuiera donc sur les voiles sans pour autant en déborder.
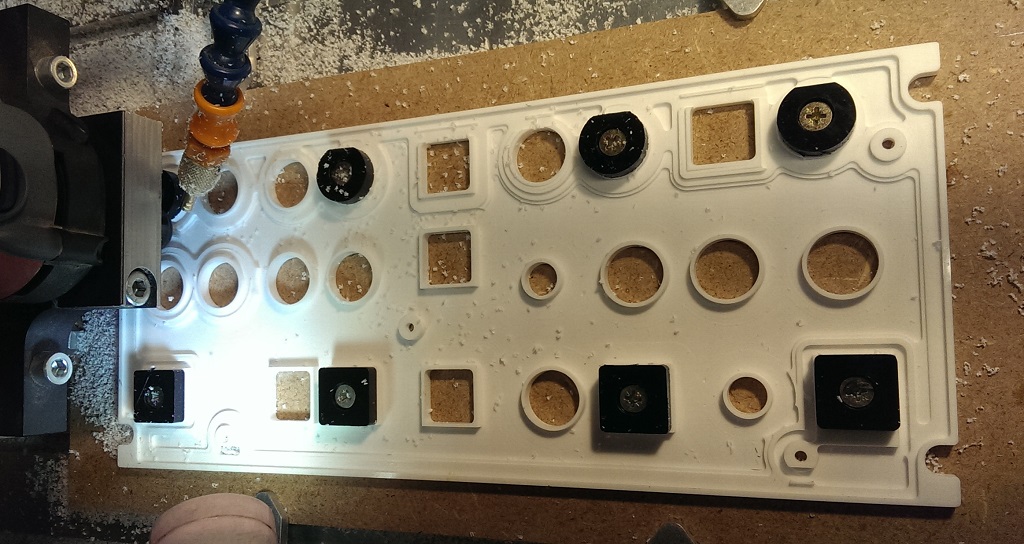
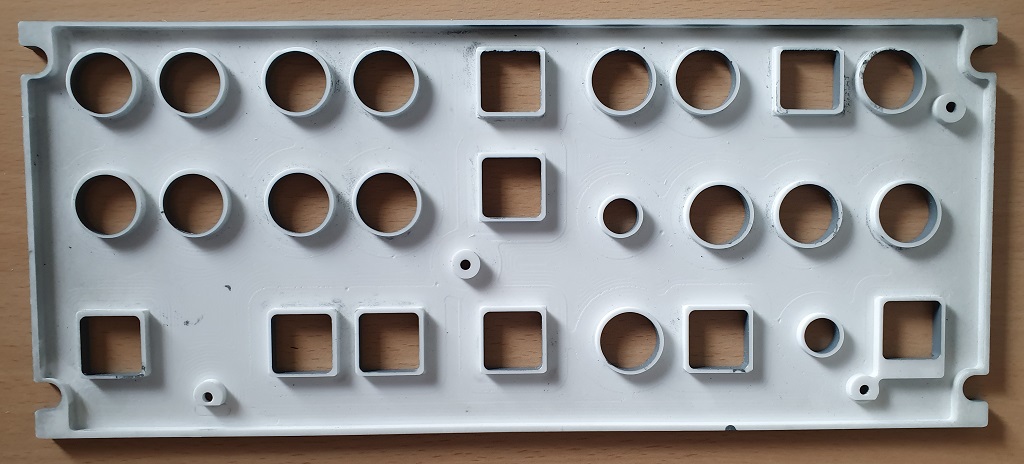
– le guide de lumière : découpe du guide et de ses ouvertures dans du PMMA transparent de 4, lamage de 8.1 mm de large et 2 de profondeur tout autour pour les bandes de leds, puis retournement pour la gravure du réseau de diffraction ; le problème du levelling se pose de la même façon que pour la face avant, et je dois à nouveau procéder à plusieurs reprises ; c’est très long, de l’ordre de 2 heures, comme pour la face avant ; ça n’est qu’après coup que je réalise que j’aurai pu réaliser la gravure avant la découpe, évitant ce problème (ce qui n’est pas le cas pour la face avant, car les ouvertures, qui sont peintes, doivent être réalisées avant gravure, puisque celle-ci intervient après peinture !).
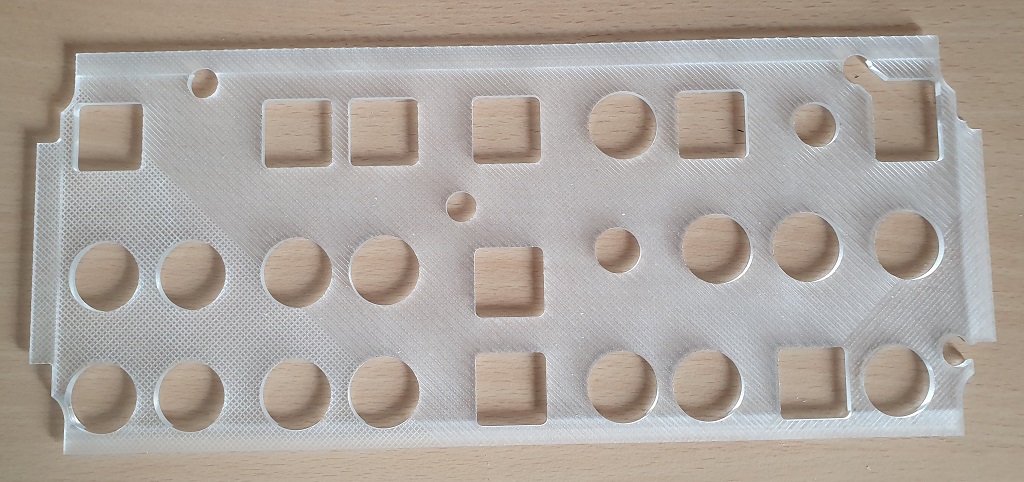
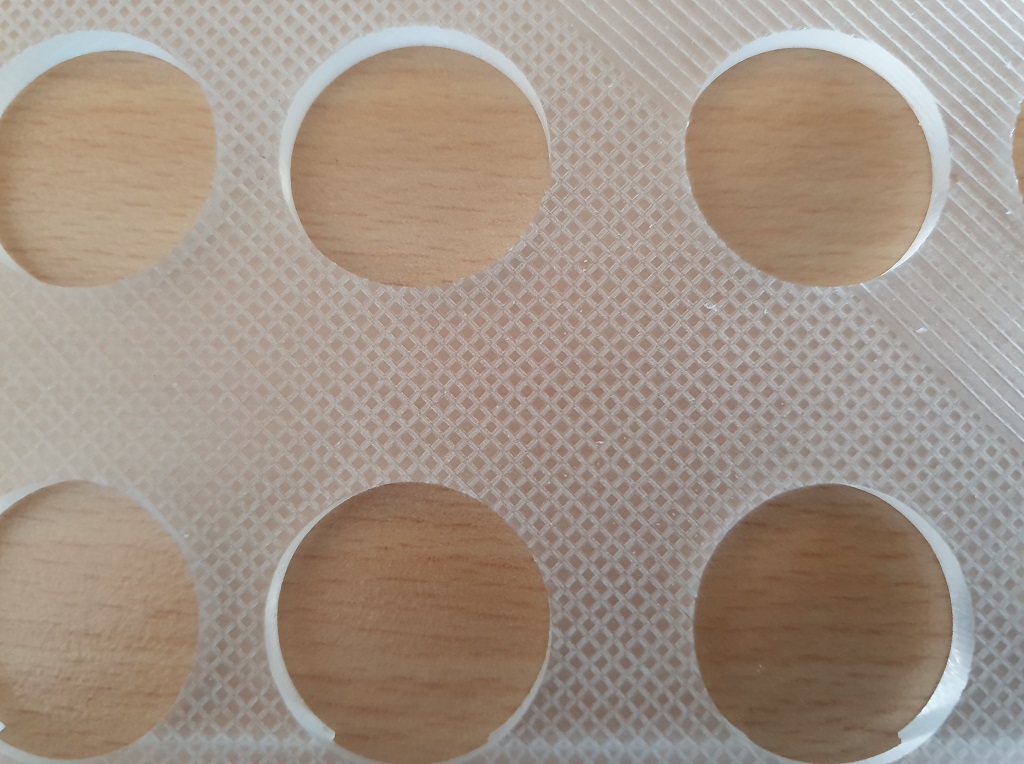
– première intégration : 4 bandes de leds vont venir ceinturer le guide de lumière, qu’il va falloir alimenter en 12 V ; pour assurer la connexion de ces bandes entre-elles , je réalise 4 petits pcbs de liaison (gravure à l’anglaise) ; le guide de lumière est mis en place dans la face avant, et les 4 bandes reliées par leur petits pcbs ; la soudure est délicate, car elle intervient à la jointure approximative de l’extrémité de la bande et de celle du pcb, il faudra trouver mieux.
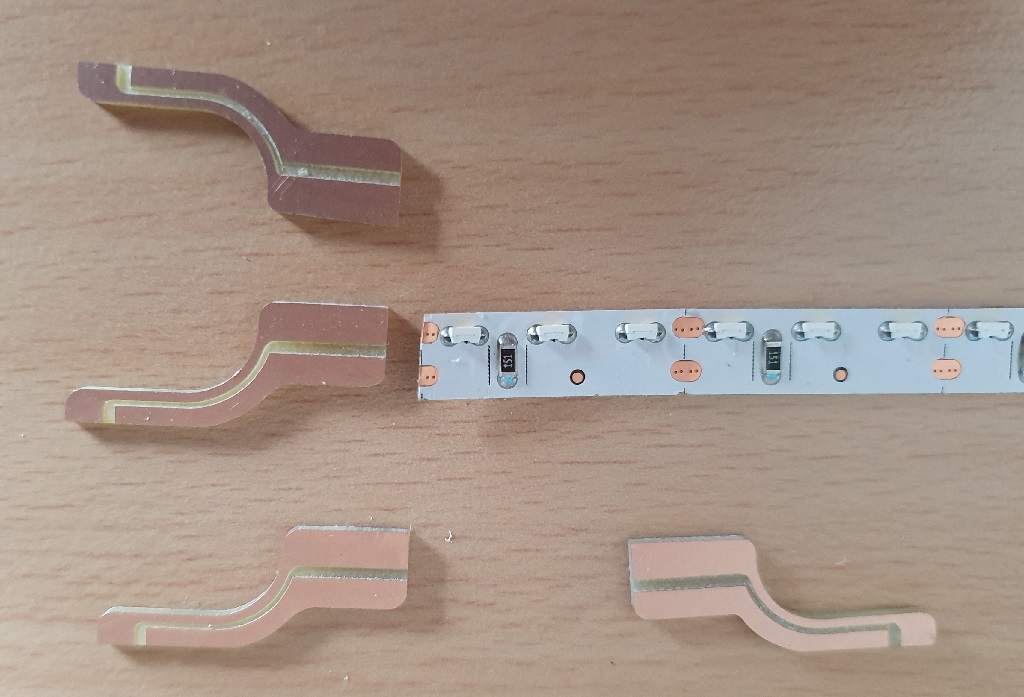
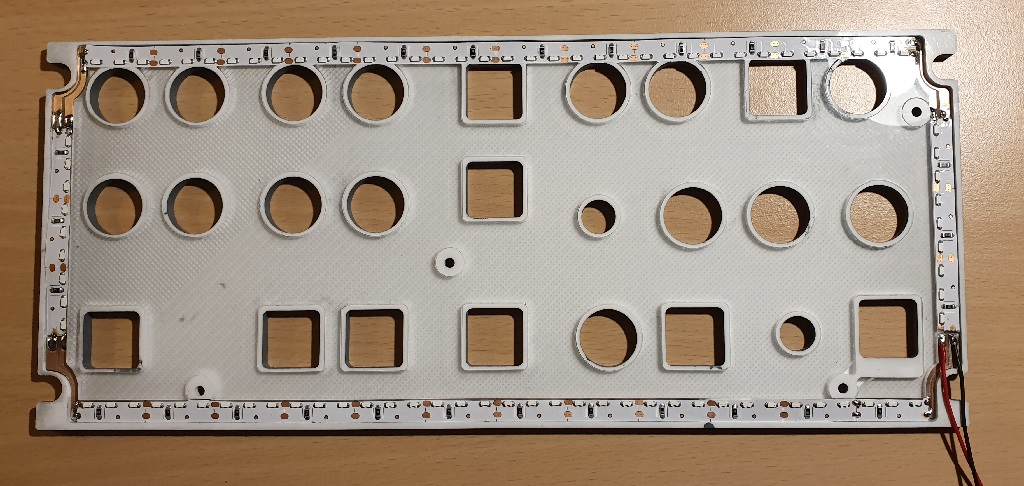
– finalisation : peinture blanche au dos du guide de lumière, rajout dans les trous des korrys des jupes supérieures des korrys (les petites pièces grises) qui, bien ajustées solidarisent faces avant et guide de lumière ;
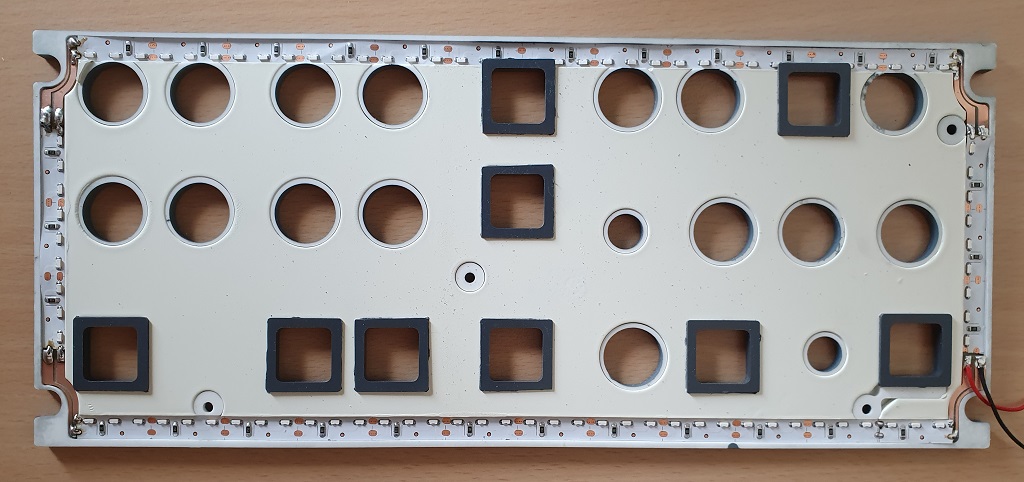
– et branchement : montage de la contre-face à l’arrière du sous-ensemble précédent, test :
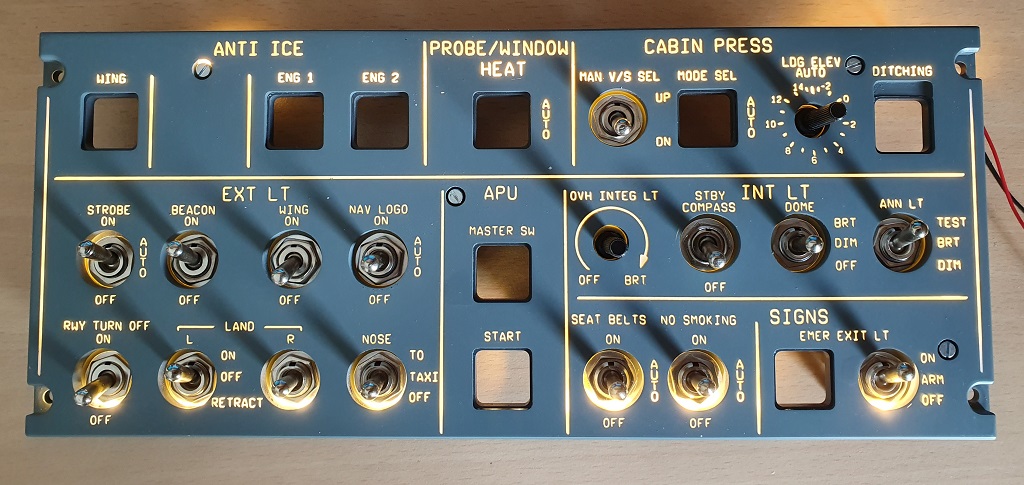
La première chose qui saute au yeux, c’est que c’est mieux qu’attendu ; c’est tellement contre-intuitif de voir que la lumière passe outre les obstacles que sont les switchs et les korrys !
A l’examen, et contrairement à ce que montre la photo (mon appareil enjolive en corrigeant, c’est de l’IA dit-on !), il y a une petite atténuation de luminosité en partie centrale, ce qui se traduit par une petite réduction apparente de la largeur des gravures, ça se remarque en particulier sur les traits verticaux ; rien de grave, mais ça se voit …
– encore un effort : je décide de rajouter 2 bandes de leds à montage à plat, donc leds directement dirigées vers la face supérieure : en effet, la gravure du guide de lumière, qui va se situer entre les leds et la face supérieure, peut opportunément jouer son rôle diffracteur et atténuer/éviter l’effet “spot” d’une led vue de face (si derrière une gravure de la face supérieure).
La disposition des ouvertures offre le passage suffisant, retour à la cnc pour 2 lamages, puis installation des 2 bandes, qui sont électriquement reliées aux bandes périphériques.
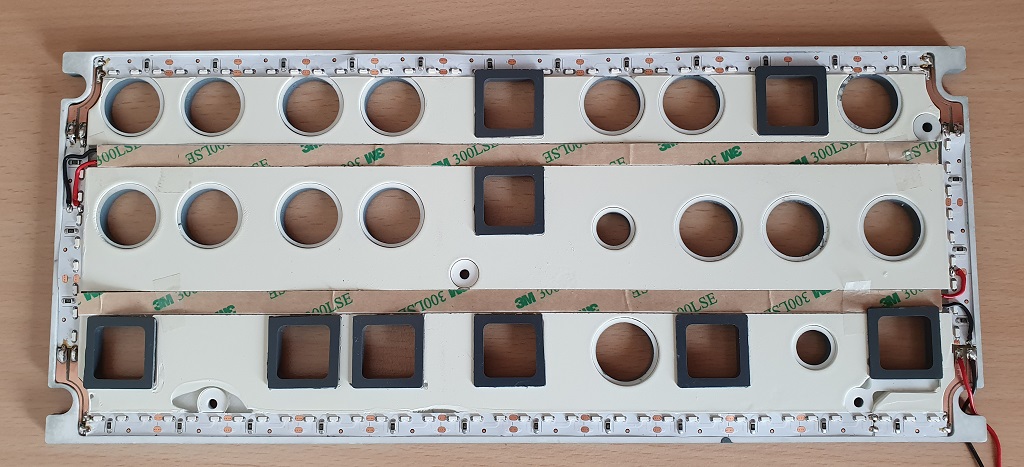
– et re-test :
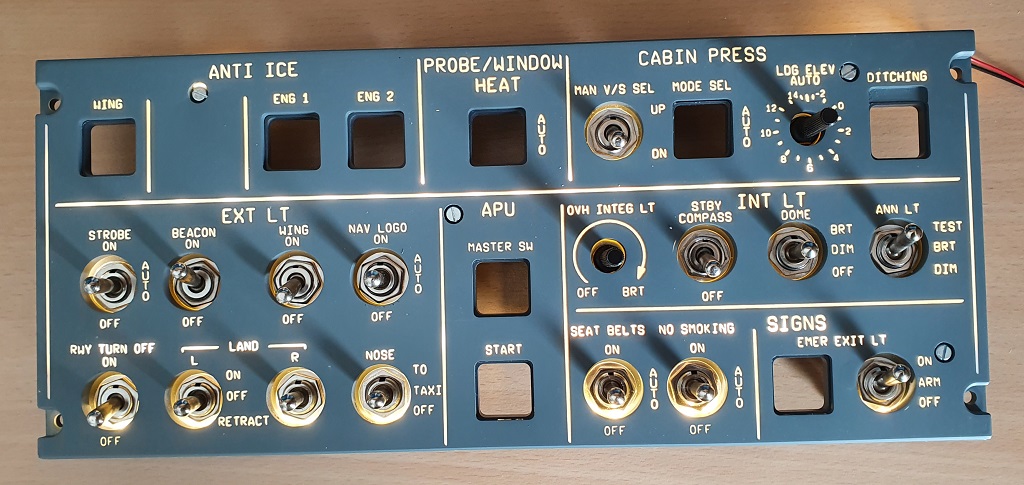
Là, c’est bon, éclairage uniforme, puissant si nécessaire (j’utilise un dimmer chinois pour alimenter en 12 v, sur la photo le dimmer est à son minimum, éclairage diurne) ; le résultat est équivallent à celui de la version 3 (avec les micro-bulbes), sans le gros inconvénient de la dissipation de chaleur, solution également plus facilement (ou plutôt moins difficilement) réalisable.
Il y a cependant un bémol : cette formule impose de pouvoir disposer des bandes de led transversalement ainsi que tout autour du panel ; il faut donc que la disposition des ouvertures le permette, et en particulier, qu’il y ait tout autour du panel une zone libre de toute ouverture de au moins 11 mm ; or, pour l’A320, qui est l’avion que je connais un peu, ça n’est pas le cas, la distance bord de panel à ouverture intérieure peut n’être que de 9 mm : il faut donc, dans le design des panels, consentir à modifier très légèrement la disposition des ouvertures, ce qui, de mon point de vue, est très peu perceptible et en rien choquant …
3 - Conclusion :
5 formules :
– v1, leds sur paneau à l’arrière de l’instrument (presque tout le simu est ainsi réalisé) : très simple à mettre en oeuvre, résultat moyen, le câblage gènant la propagation de la lumière vers la face avant (ça n’en est pas moins tout à fait crédible).
– v2, leds sur pcb derrière la contre-face (2 panels du simu) : bon résultat sauf si gros dispositif en face avant gênant la propagation de la lumière ; rétro-éclairage non intégré.
– v3, micro-bulbes et peinture blanche + peinture grise en face avant, gravure de la seule peinture grise (1 panel réussi) ; très bon résultat mais grosse dissipation de chaleur ; très compliqué à réaliser.
– v2 bis, leds sur pcb encastré (1 panel réussi) : très bon résultat, mais sous-traitance presque incontournable.
– v4 bis, leds en éclairage latéral (2 panels réussis) : très bon résultat, contrainte géométrique, réalisation niveau confirmé.
J’aime bien la dernière, en plus à ma connaissance c’est plutôt une première !
Février 2020